Green Aviation entails activities aimed at increasing aircraft fuel efficiency, developing the next generation of efficient air traffic control, and developing new technologies and systems engineering processes in order to achieve the global goal of carbon-neutral air transportation.
Experts have discovered a method for fine-tuning the strength and ductility of a class of materials known as high-entropy alloys. The discovery could aid in the development of more efficient engines in the power generation and aviation industries.
Computational materials scientists at the U.S. Department of Energy’s Ames Laboratory and their collaborators have discovered the source of, and method for tuning, the strength, and ductility of a class of materials known as high-entropy alloys. The discovery could aid in the development of more efficient engines in the power generation and aviation industries, reducing fuel consumption and carbon emissions.
When we can pinpoint these transformations and the effect they have on a material’s properties, we can predict its strength and design strength, and ductility into these very complex alloys.
Duane Johnson
High-entropy alloys are made up of four or more different elements and have many desirable properties, including being lightweight, strong, ductile, corrosion resistant, and ideal for energy-generation applications in extreme environments, such as aviation. However, because the elements that make up an alloy can vary, as can their relative proportions, testing the vast number of possible combinations and their properties is difficult and time-consuming.
The team led by Ames Laboratory used a quantum-mechanical modeling method to discover and predict the atomic structure of a particularly promising HEA system, FexMn80-xCo10Cr10, as well as how transformations and defects in that structure result in a stronger, more ductile material.
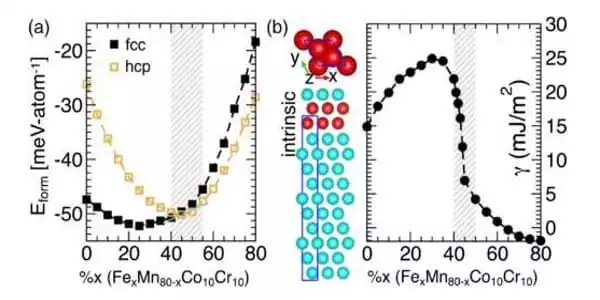
Complex metallic alloys are a catch-all term for intermetallic compounds with a large unit cell. There is no precise definition of how large a complex metallic alloy’s unit cell must be, but the broadest definition includes Zintl phases, Skutterudites, and Heusler compounds on the simple end and quasicrystals on the more complex end.
“When we can pinpoint these transformations and the effect they have on a material’s properties, we can predict its strength and design strength and ductility into these very complex alloys,” said Duane Johnson, an Ames Laboratory scientist. These predictions were then tested experimentally by using advanced electron microscopy on single-crystal samples, including selective-area and electron-backscattered diffraction. It is worth noting that the method is applicable to any multi-element complex alloy.
Materials with complex custom internal structures can be created using modern fabrication techniques such as additive manufacturing. These engineered materials, known as meta materials or microstructures, have a much broader range of bulk properties than their base materials. Although meta materials with extraordinary properties have a wide range of applications, designing them is difficult and is typically done by hand.
According to Johnson, theory-guided computational design holds great promise for improving the performance of these materials, making them stronger, more ductile, and, in many cases, less expensive. These performance gains could have significant implications for applications in extreme environments, such as turbine engines for power generation or aviation, which operate more efficiently at higher temperatures.
“By using this predictive method, we were able to cut our alloy development timeline by more than half and demonstrate 10-20% higher operational temperatures,” Johnson said. In the case of aviation, he claims that this could result in hundreds of millions of dollars in cost savings as well as a significant reduction in greenhouse gas emissions.