Until now, wastewater treatment plants haven’t been able to filter out microscopic microplastics in wastewater effectively, but that may change soon: At a wastewater treatment plant, the first laser-drilled microplastic filter is being tested. It includes sheets with holes as small as 10 micrometers in diameter. The Fraunhofer Institute for Laser Capability ILT developed the technology to drill millions of such holes efficiently, and now the institute’s engineers are scaling up ultrashort-pulse (USP) laser technology in the kW range. At the Fraunhofer stand A6.441 at LASER World of PHOTONICS, visitors may learn more about the microplastic filter and ultrashort-pulse lasers.
Sustainability is no longer a choice, but rather a need, regardless of the technology in development. As a result, the laser industry is rapidly incorporating USP technology into numerous projects to promote sustainability. Lasers are already being used in electromobility applications to improve the efficiency of hydrogen technology and to create incredibly tight battery housings.
“At its core, our challenge was to drill as many holes as possible, as small as possible, in a steel foil in the shortest time possible,”
Andrea Lanfermann, project manager at Fraunhofer ILT.
For the first time, Fraunhofer ILT collaborated with industrial partners on the BMBF-funded “SimConDrill” project to develop a filter that can remove microplastics from wastewater for the first time. “Our aim was to drill as many microscopic holes as possible in a steel foil in the shortest time feasible,” Andrea Lanfermann, project manager at Fraunhofer ILT, explains.

In a wastewater treatment plant, a mobile filter plant is used.
This was accomplished. Experts at LaserJob GmbH drilled 59 million holes with a diameter of 10 micrometers into a filter sheet, creating a filter prototype after the technology was invented at Fraunhofer ILT. In this big endeavor, Fraunhofer experts are collaborating with three other companies. In addition to the project coordinator, KLASS Filter GmbH, LUNOVU GmbH, and OptiY GmbH are also involved.
Meanwhile, the laser-drilled metal foils have been placed and thoroughly tested in KLASS Filter GmbH’s revolutionary cyclone filter. In the first test, the fine powder from 3D printers was filtered from contaminated water. The system is now being tested in a wastewater treatment plant in real-world settings.
Process understanding is essential.
Drilling millions of holes one by one takes time, but it may be done faster with the multibeam technique, which uses a sophisticated optical system to generate a matrix of similar beams from a laser beam. Fraunhofer ILT used an ultrashort-pulse laser (TruMicro 5280 Femto Edition) to drill holes with 144 beams concurrently. Detailed process knowledge, gathered over decades at Fraunhofer ILT and incorporated into related models and software, serves as the foundation for such applications. Due to this skill, parameters may be adjusted on the computer, and the best process parameters can be identified rapidly. Before the application is evaluated, the process’s robustness can be assessed.
A collaboration of six partners is working on how to best incorporate a multi-beam processing system into an industrial machine in parallel with this drilling application. Researchers and industry partners are working together on the EU project “Multiflex” to improve the productivity of scanner-based laser material processing using multi-beam methods. This project is unique in that every partial beam can be individually controlled and hence used to create any type of surface structure. The project partners hope to boost the process’ speed by a factor of twenty to fifty, making the overall process far more cost-effective.
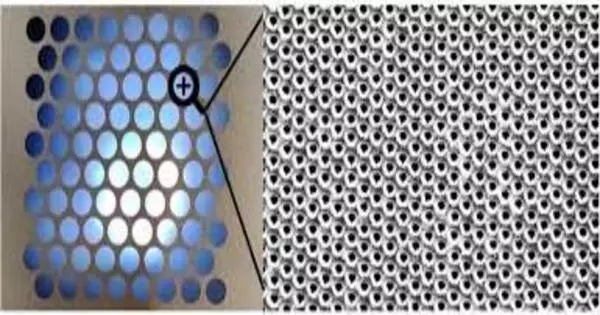
Scaling into the kW range with CAPS
Process knowledge is also important for scaling up ultrashort laser pulses with or without multibeam optics for materials processing. Thermal damage to the workpiece might occur when power is increased in the kilowatt range. Complex simulations are used to investigate such effects, and processes can be adjusted accordingly.
In the application laboratory at Fraunhofer ILT in Aachen, laser systems for such studies are accessible. They’re part of the Fraunhofer Cluster of Excellence Advanced Photon Sources (CAPS), which brings together 13 Fraunhofer institutes to work on laser beam sources, process technologies, and applications for USP lasers with powers up to 20 kW. Fraunhofer IOF in Jena operates a second CAPS laboratory.
Fraunhofer expertise is on display at the LASER World of PHOTONICS.
The laser-drilled microplastic filter, as well as other highlights of the Fraunhofer Cluster of Excellence Advanced Photon Sources CAPS, will be on display at the leading photonics trade fair, Laser World of PHOTONICS, in Munich from April 26 to 29, 2022. Experts will be available at the Fraunhofer booths A6.441 and B4.239 to provide information about ultrashort pulse laser technology, the generation of secondary radiation from THz to X-rays, and its groundbreaking applications.