With no corrosive chemicals, high temperatures, or prior material sorting necessary, a recycling technique created by the Karlsruhe Institute of Technology (KIT) can recover up to 70% of lithium from battery waste. The technique combines mechanical and chemical processes and makes it possible to recycle any kind of lithium-ion battery at a low cost with minimal energy consumption. Communications Chemistry publishes the findings.
We constantly surround ourselves with lithium-ion batteries. They are the most crucial energy storage systems for the quickly expanding electric mobility sector, as well as for the wireless power supply of laptops, smartphones, toys, remote controls, and other small devices. The need for recycling techniques that are both economically and environmentally viable arises as the use of these batteries increases.
“The process can be used to recover lithium from cathode materials of varied chemical compositions, and therefore for a wide range of commercially available lithium-ion batteries,”
Dr. Oleksandr Dolotko of IAM-ESS and HIU, the first author of the publication.
At the moment, metals recovered for reuse from battery waste include mainly nickel and cobalt, copper and aluminum, as well as steel. The cost and lack of profitability of lithium recovery persist. Most current recovery techniques have a metallurgical nature, are energy-intensive, and/or result in dangerous by-products. Mechanochemical methods, which rely on mechanical processes to trigger chemical reactions, have the potential to produce higher yields and be more cost-effective than other methods.
Suitable for a variety of cathode materials.
A method of this kind has now been developed by the Energy Storage Systems Department of KIT’s Institute for Applied Materials (IAM-ESS), the Helmholtz Institute Ulm for Electrochemical Energy Storage (HIU), which was founded by KIT in collaboration with Ulm University, and EnBW Energie Baden-Württemberg AG.
Without using corrosive chemicals, extreme temperatures, or pre-sorting of materials, the method achieves a lithium recovery rate of up to 70%. The first author of the study, Dr. Oleksandr Dolotko of IAM-ESS and HIU, says that the technique can be used to recover lithium from cathode materials with a variety of chemical compositions and, consequently, for a wide range of commercially available lithium-ion batteries. “It makes recycling affordable, energy-efficient, and environmentally friendly possible.”.
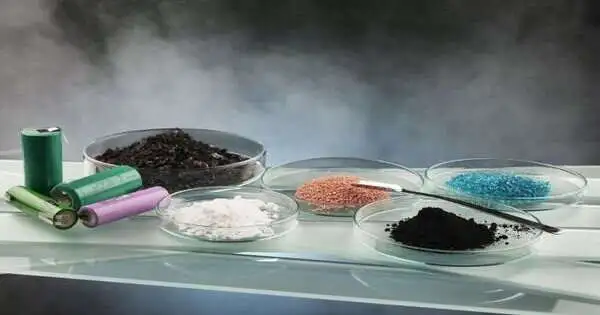
The more batteries that can be recycled, the more crucial sustainable recycling processes for the recyclable materials they contain become. Credit: Amadeus Bramsiepe, KIT
Reaction that takes place at room temperature.
As a reducing agent in the mechanochemical reaction, aluminum is used by the researchers. There is no need for extra materials because aluminum is already present in the cathode. The process begins with the grinding of the used battery material. Then, this substance reacts with aluminum to create metallic composites that contain lithium compounds that are soluble in water.
These compounds are dissolved in water to recover the lithium, which is then heated to cause the water to evaporate. The method is very energy-efficient because the mechanochemical reaction occurs at ambient pressure and temperature.
Another benefit is its simplicity, which will make it easier to use on an industrial scale since a lot of batteries will need to be recycled in the near future.
More information: Oleksandr Dolotko et al, Universal and efficient extraction of lithium for lithium-ion battery recycling using mechanochemistry, Communications Chemistry (2023). DOI: 10.1038/s42004-023-00844-2