Fostering a lightweight material that is both profoundly bendable and strong has been viewed as a long-wanted objective in the field of primary materials, yet these properties are, for the most part, totally unrelated. Specialists at City College of Hong Kong (CityU) have as of late found a minimal expense, direct strategy to transform normally utilized 3D printable polymers into lightweight, super-extreme, biocompatible half-breed carbon microlattices, which can be in any shape or size, and are multiple times more grounded than the first polymers. The examination group accepts that this inventive methodology can be utilized to make modern 3D parts with customized mechanical properties for many applications, including coronary stents and bio-inserts.
Metamaterials are materials designed to have properties that are not tracked down in normally occurring materials. 3D-architected metamaterials, like microlattices, consolidate the advantages of lightweight underlying model standards with the characteristic properties of their constituent materials. Making these microlattices frequently necessitates advanced creation advances, for example, added substance production (also known as 3D printing), yet the scope of materials available for 3D printing is still extremely restricted.
3D printing is turning into a pervasive innovation for creating mathematically complex parts with special and tunable properties. Solid and extreme architected parts typically require metals or amalgams to be 3D-printed. However, they are not effectively available, inferable from the significant expense and low goal of business metal 3D printers and unrefined components. Polymers are more available yet regularly need mechanical strength or durability. “We figured out how to change these more vulnerable and fragile 3D-printed photopolymers into super extreme 3D structures practically identical to metals and composites by simply warming them under the right circumstances, which is astounding,” said Teacher Lu Yang of the Branch of Mechanical Designing (MNE) and Division of Materials Science and Designing (MSE) at CityU, who drove the examination.
The different mechanical ways of behaving of, to some degree, carbonized structures are contrasted with the first polymer structure. The scale bars address 2mm.
Up until this point, the best methodology for expanding the strength of these 3D-printable polymer cross sections was pyrolysis, a warm treatment that changes the whole polymer into super impressive carbon. Nonetheless, this interaction denies the first polymer cross section of practically the entirety of its deformability and produces an incredibly weak material, similar to glass. Different strategies to build the strength of the polymers also regularly lead to undermining their flexibility.
“Our work provides a low-cost, easy, and scalable technique for producing lightweight, strong, and ductile mechanical metamaterials with nearly any geometry,”
Professor Lu.
The group driven by Teacher Lu saw an “enchantment like” condition in the pyrolysis of the 3D-printed photopolymer microlattices, which brought about a 100-overlay expansion in strength and multiplied the flexibility of the first material. Their discoveries were published in the logical journal Matter under the title “Lightweight, Super-extreme 3D Architected Half and Half Carbon Microlattices.”
They found that by cautiously controlling the warming rate, temperature, span, and gas climate, it is feasible to upgrade the firmness, strength, and pliability of a 3D-printed polymer microlattice in a solitary step at the same time.
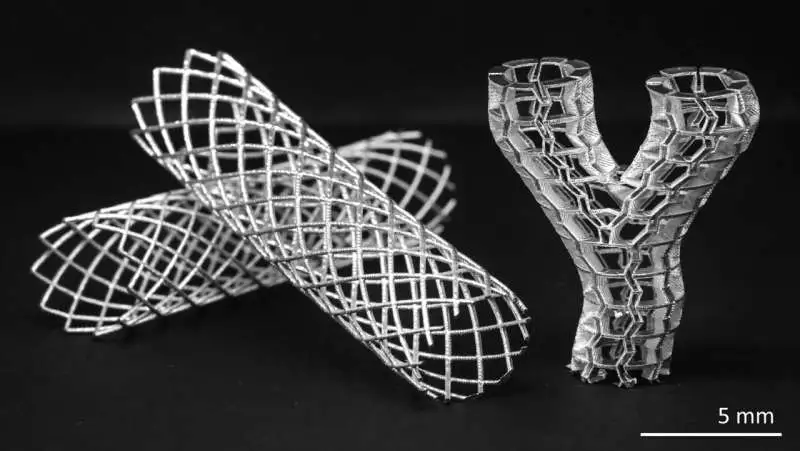
Demo of coronary stents with a 3D-printed, to some degree, carbonized center. Credit: James Utama Surjadi et al., Matter (2022). DOI: 10.1016/j.matt.2022.08.010
Through different portrayal strategies, the group observed that concurrent improvement in strength and pliability is conceivable just when the polymeric chains are “to some extent carbonized” by sluggish warming, where deficient transformation of the polymer chains to pyrolytic carbon happens, creating a half-breed material where both freely cross-connected polymer chains and carbon sections synergistically coincide. The carbon pieces act as supporting specialists that fortify the material, while the polymer chains limit the cracking of the composite.
The proportion of polymer to carbon sections is additionally pivotal to getting ideal strength and malleability. Assuming there are such a large number of carbon parts, the material becomes fragile, and in the event that there are too few, the material needs strength. During the trials, the group effectively made an ideally carbonized polymer cross section that was north of 100 times more grounded and north of two times more flexible than the first polymer grid.
Benefits beyond mechanical property improvement
The exploration group additionally saw that these “mixture carbon” microlattices showed further developed biocompatibility compared with the first polymer. Through cytotoxicity and cell conductivity checking tests, they demonstrated that the cells refined on the half-bred carbon microlattices were more reasonable than cells cultivated on the polymer microlattices. The upgraded biocompatibility of the cross-bred carbon grids suggests that the advantages of halfway carbonization might go past improvement in mechanical execution and possibly work on different functionalities too.
“Our work gives a minimal expense, basic and versatile course for making areas of strength for lightweight bendable mechanical metamaterials with practically any calculation,” said Teacher Lu. He imagines that the recently designed approach can be applied to different sorts of utilitarian polymers and that the mathematical adaptability of these architected mixtures of carbon metamaterials will permit their mechanical properties to be customized for many applications, for example, biomedical inserts, precisely strong frameworks for miniature robots, and energy-reaping and stockpiling gadgets.
Teacher Lu is the comparing creator, and Dr. James Utama Surjadi, a postdoc in his group, is the primary creator of the paper. Associate Teachers include Teacher Wang Zuankai, Seat Teacher in the MNE Office, and Dr. Raymond Lam Hiu-wai, Partner Head and Academic Administrator in the Branch of Biomedical Designing of CityU.
More information: James Utama Surjadi et al, Lightweight, ultra-tough, 3D-architected hybrid carbon microlattices, Matter (2022). DOI: 10.1016/j.matt.2022.08.010
Journal information: Matter