Before the end of last year, Caltech specialists uncovered that they had fostered another manufacturing method for printing micro sized metal parts containing highlights probably as thick as three or four pieces of paper.
Presently, the group has reexamined the strategy to consider printing objects multiple times more modest: 150 nanometers, which is practically identical to the size of a seasonal infection. In doing so, the group additionally found that the nuclear game plans inside these articles are confused, which would, on a large scale, make these materials unusable in light of the fact that they would be viewed as powerless and “bad quality.” On account of nanosized metal items, in any case, this nuclear-level wreck makes the opposite difference: these parts can be three-to-five times more grounded than comparably estimated structures with additional deliberate nuclear courses of action.
The work was led in the lab of Julia R. Greer, Ruben F., Donna Mettler, Teacher of Materials Science, Mechanics, and Clinical Designing, and Fletcher Jones, Establishment Head of the Kavli Nanoscience Foundation. The paper portraying the work, “Stifled Size Impact in Nanopillars with Progressive Microstructures Empowered by Nanoscale Added Substance Assembling,” is distributed in the August issue of Nano Letters.
“In metal nanopillars, the deformation carrier—that is, a dislocation or slip—usually propagates until it can escape at the outer surface. However, in the presence of internal pores, propagation will immediately end at the surface of a pore rather than continuing all the way through the pillar. As a general rule, it is more difficult to nucleate a deformation carrier than to allow it to propagate, which explains why the current pillars may be stronger than their counterparts.”
Says Wenxin Zhang, lead author of the work and a graduate student in mechanical engineering.
The new method is like one more declared by the group last year, yet with each step of the interaction reconsidered to work at the nanoscale. Nonetheless, this presents an extra test: the fabricated items are not apparent to the unaided eye or effectively manipulatable.
The cycle begins with setting up a photosensitive “mixed drink” that, to a great extent, contains a hydrogel, a sort of polymer that can normally retain its own load in water. This mixed drink is then specifically solidified with a laser to fabricate a 3D platform in similar shape to the ideal metal items. In this examination, those items were a progression of little points of support and nanolattices.
The hydrogel parts are then imbued with a watery arrangement containing nickel particles. When the parts are immersed with metal particles, they are heated until all the hydrogel is worn out, leaving parts in a similar shape as the first, however contracted, and comprising completely metal particles that are currently oxidized (bound to oxygen iotas). In the last step, the oxygen iotas are synthetically stripped out of the parts, changing the metal oxide back into a metallic structure.
In the last step, the parts foster their surprising strength.
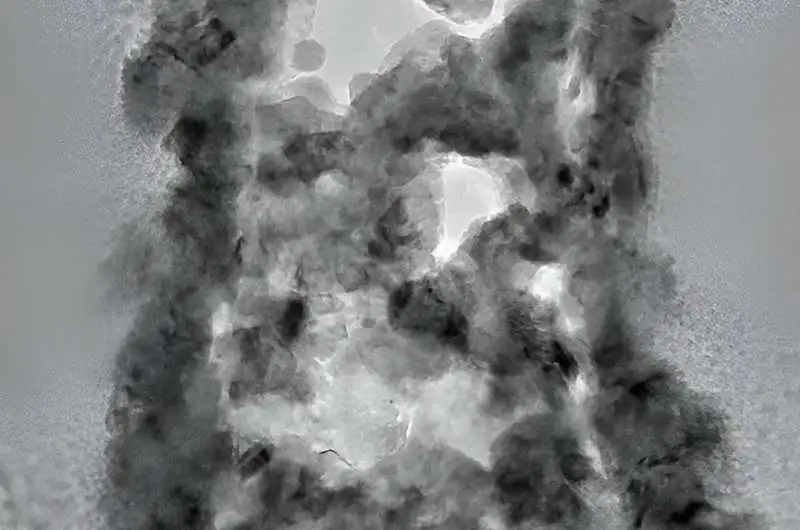
The unpredictable inside construction of a nanoscale nickel point of support Credit: Caltech
“There are these warm and motor cycles happening all the while during this interaction, and they lead to an incredibly untidy microstructure,” she says. “You see abandons like pores and abnormalities in the nuclear construction, which are commonly viewed as strength-disintegrating absconds. If you somehow happened to fabricate something out of steel, say, a motor block, you would have zero desire to see this kind of microstructure in light of the fact that it would fundamentally debilitate the material.”
In any case, Greer says they saw the very opposite. The many imperfections that would debilitate a metal part at a larger scale reinforce the nanoscale parts, all things considered.
At the point when a point of support is without deformity, disappointment happens devastatingly along what is known as a grain limit—where the minuscule gems that make up material run into one another.
However, when the material is brimming with deserts, disappointment can only be spread with significant effort, starting with one grain limit and then onto the next. That implies the material will not, out of nowhere, fizzle in light of the fact that the deformity becomes conveyed all the more uniformly throughout the material.
“Generally, the distortion transporter in metal nanopillars—that is, a disengagement or slip—engenders until it can escape at the external surface,” says Wenxin Zhang, the lead creator of the work and an alumni understudy in mechanical design. “Be that as it may, within the sight of inside pores, the spread will rapidly end at the outer layer of a pore as opposed to proceeding with the whole way through the whole point of support. As a guideline, it’s harder to nucleate a twisting transporter than to allow it to engender, making sense of why the current points of support might be more grounded than their partners.”
Greer accepts that this is quite possibly the earliest exhibition of 3D printing of metal designs at the nanoscale. She takes note that the cycle could be utilized for making numerous valuable parts, like impetuses for hydrogen; capacity cathodes for carbon alkali and different synthetics; and fundamental pieces of gadgets like sensors, microrobots, and heat exchangers.
“We were initially stressed,” she says. “We thought, ‘Gracious my, this microstructure is never going to prompt anything great,’ yet obviously, we didn’t have an excuse to be stressing out in light of the fact that it turns out it’s not so much as an impediment. It’s really an element.”
More information: Wenxin Zhang et al, Suppressed Size Effect in Nanopillars with Hierarchical Microstructures Enabled by Nanoscale Additive Manufacturing, Nano Letters (2023). DOI: 10.1021/acs.nanolett.3c02309