Current pyroprocessing methods vow to provide locally obtained atomic fuel at a reasonable expense for cutting-edge reactors while radically reducing the volume and harmfulness of the excess waste.
For countless years, only a small percentage of the uranium in a light water reactor fuel bar is utilized to create energy before the poles are taken out of the reactor and put into long-lasting stockpiling, leaving the spent atomic waste (SNF) to keep on rotting at a somewhat high harmfulness rate for countless years.
Work on reusing SNF—simply under 33% of the nearly 400,000 tons created worldwide has been gone back over—has seen blended results, delivering possibly risky weapons-grade materials at an expense that is essentially higher than mining more uranium.
The current overall going back over limit is just shy of 2,000 tons per year through plants in France, Britain, India, and Russia.
Following the Russian intrusion into Ukraine, getting a homegrown fuel supply for U.S. atomic reactors has turned into a need, and one line of exploration shows up particularly encouraging for cutting-edge atomic reactors right now being developed.
“To increase efficiency, we are combining some of the next generation sensors that we have created with process control. We’re seeking to improve the product gathering approach, reduce the cost of the operations, and employ technology such as machine learning.”
Argonne’s Pyroprocess Engineering section manager Krista Hawthorne.
Researchers at the U.S. Argonne National Laboratory started dealing with reusing quick reactor fuel in the mid-sixties during the improvement of the Experimental Breeder Reactor-II (EBR-II) and later during the Integral Fast Reactor (IFR) program.
Argonne has expanded work that started with the EBR-II, a quick neutron reactor, to foster pyrochemical cycles for the reuse of oxide, carbide, and other high-level fuels.
The IFR, a fluid metal-cooled quick reactor, was subsequently intended to create energy and consume squander. Keeping in mind that dealing with it, scientists embraced a pyroprocess by which an electrochemical response is utilized to isolate the ideal actinides from the undesired parting items for reuse into new fuel.
“At this moment, our center is moving pyroprocessing to a prepared to-send state,” says Argonne’s Pyroprocess Engineering segment chief, Krista Hawthorne.
Pyroprocessing and electrorefining
Pyroprocessing converts the oxide constituents of hard clay oxide pellets recovered from light water reactors—roughly 95% of which is still uranium, another 1% is enduring radioactive components actinides, and the rest is unusable parting items—into metal.
That metal is then lowered into a tank of liquid salt where, through electrorefining, an electric flow specifically breaks up and redeposits uranium and other reusable components, which are then used to create fuel that can be utilized by quick reactors.
4% of the fuel that is unusable parting items actually should be discarded through long-lasting stockpiling. However, its radioactive harmfulness returns to levels of normally occurring uranium inside a couple hundred years, which is not exactly the length of time untreated SNF takes to return on the grounds that the majority of the enduring isotopes have been reused.
The relative radiological harmfulness of utilized fuel constituents
Today, LWRs remain the standard plan for atomic reactors in the United States, for which crude uranium is a modest and promptly accessible fuel, yet as quick reactors draw nearer to show and, before the decade’s over, business reception, reused fuel could be the standard.
Through broad work on the financial matters of fuel reusing, Argonne’s 2018 review, “Calculated Design of a Pilot-Scale Pyroprocessing Facility,” focuses on the suitability of electrorefining as a viable answer for involved fuel reusing and quick reactors.
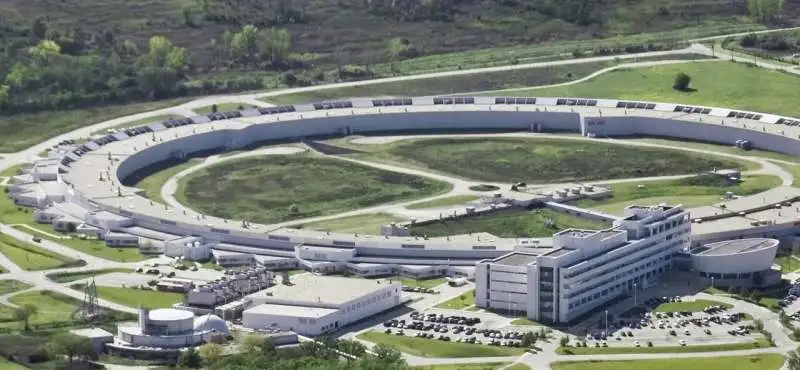
Argonne National Laboratory research offices.
In the exploration, a framework intended to reuse 100 tons of fuel a year had an all-out capital expense of $398 million, including process gear and emotionally supportive networks, assessed to cost $93 million, and an office cost of $305 million.
Increasing to 400 tons a year was assessed to run at an all-out capital expense of $911 million and a yearly working expense of $90 million.
Since the review’s delivery, Argonne has been enhancing that plan to take it to a monetarily suitable level utilizing the most recent innovation.
“We’re doing things like, for example, coordinating a portion of the cutting edge sensors that we’ve created with process control to work on the proficiency. We’re taking a gander at further developing the item assortment strategy, bringing down the expense of the cycles, and we’re likewise utilizing methods like AI, “says Hawthorne.
Argonne is fostering a computerized twin of the electrorefiner that takes criticism from in-house created checking sensors so the group can recognize and respond to changing electrorefining conditions continuously.
“We’re working diligently to work on the proficiency and work toward industrialization of pyroprocessing,” she says.
Oklo ready
Argonne’s work, accompanied by microreactor designer Oklo, has gotten the attention of the U.S. Branch of Energy (DOE).
Oklo’s pioneers CEO Jacob DeWitte and COO Caroline Cochran, as well as Argonne Lab Director Paul Kearns, paid a visit to U.S. Secretary of Energy Jennifer Granholm in August through the organization’s trial programs at Argonne.
The California-based designer has been granted $11.5 million for three DOE serious honors, diverted through the Technology Commercialization Fund (TFC), ARPA-E OPEN and ARPA-E ONWARDS, to foster high-level reusing advances in association with Argonne.
Oklo was likewise granted an award through the Gateway for Accelerated Innovation in Nuclear (GAIN) for trial fluid metal warm water driven work at Argonne’s new Mechanisms Engineering Test Loop (METL) office.
The organization, which has a site use grant from the DOE to fabricate its most memorable plant at Idaho National Laboratory (INL) and fostered the main high-level parting joint permit application, says it is on target to send its most memorable business progress reactor in the United States by 2025.
Cutting edge quick reactors, like Oklo’s Aurora, are supported by reusing utilized fuel, thus offering a truly necessary answer for shutting down the atomic fuel cycle.
“At this moment, squander is an immense risk and there’s huge consumption just to store it, so if somebody somehow managed to pay us to get it from them, then that changes the financial matters. Regardless of whether it’s free, it’s as yet useful and monetary, “says COO Cochran.
The ongoing worry over the expense of reusing is unwarranted, says Cochran, particularly while filling cutting-edge quick reactors like Oklo’s Aurora, TerraPower’s Natrium or liquid salt reactors from Moltex and Elysium.
“There’s no great explanation for why it ought to be so costly. It’s the way you work and manage it. Fuel is our greatest single expense. “In the event that we can reuse it, then we can truly accomplish costs that are lower than anything on the matrix today,” she says.
Provided by Argonne National Laboratory