Lighter vehicles can travel farther on less energy, driving interest in lighter auto parts. Elite execution aluminum combinations, for example, compound 7075, are among the lightest and most grounded choices, but they require energy-concentrated creation that raises costs and, in this manner, restricts their utilization.
Research from the Pacific Northwest National Laboratory (PNNL) slices that energy down the middle with a more productive cycle to make elite aluminum parts. With help from the Department of Energy’s Advanced Manufacturing Office, scientists discovered that the Shear Assisted Processing and Extrusion (ShAPE) innovation can kill heat treatment steps in the creation cycle, bringing about critical energy reserve funds and decreased outflows. ShAPE is a green, reasonable assembling approach that enables expansive utilization of superior-execution aluminum compounds in auto applications.
A recipe for next-generation metals manufacturing
Metal production, like baking a cake, is dependent on a lot of blended fixings and a lot of intensity.Customary metal creation utilizes intensity to liquefy individual metals and alloying components together — like aluminum, copper, or magnesium — to make combinations that are lighter, more grounded, or simpler to frame. In the event that these components aren’t very much blended, breaks and cracks can form during handling that compromise the properties of the end result, as an undermixed, uneven cake will result in a disintegrating, grievous cake. Heat is used in metals production to ensure that individual metal components in a mixture are thoroughly blended during a stage known as homogenization.
“This is a critical step toward realizing the full promise of next-generation metals manufacturing to develop better, cheaper, greener products in the future,”
Scott Whalen, PNNL chief materials scientist and co-developer of ShAPE.
During homogenization, huge metal castings called billets are warmed to almost 500 degrees Celsius (around 900 degrees Fahrenheit) for as long as 24 hours. This intensity therapy step breaks down composite totals—similar to knots in the cake hitter—in the billet to guarantee that all metal components are equitably circulated or homogenized. This works on the exhibition of the end result. After homogenization, the metal poles go through additional warming and shaping in a stage called expulsion.
“Homogenization is the greatest energy-consuming move toward the whole metal expulsion process,” said Scott Whalen, PNNL chief materials researcher and co-designer of ShAPE.
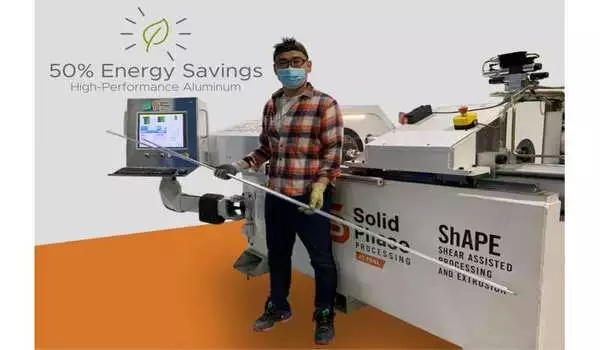
Shear Assisted Processing and Extrusion (ShAPE), created by specialists at Pacific Northwest National Laboratory, further develops the energy proficiency of delivering expelled superior-execution aluminum amalgams.
The ShAPE machine wipes out the requirement for discrete homogenization and expulsion ventures by joining warming and twisting—the adjustment of the state of the actual metal. In the ShAPE machine, the metal billet is all the while pushed through a little opening in the dust which turns. Together, the rotational development and twisting completely blend the metal components as they are being expelled. Basically, the ShAPE cycle homogenizes the metal billet briefly, prior to it being expelled. This disposes of the requirement for a day-long, pre-warming homogenization step and implies that no extra energy is utilized to warm the billet during expulsion. As a result of this, an energy reserve fund of up to 50% using ShAPE is created.
Have your cake and eat it too
In addition to the fact that shape is a more energy-efficient and speedier cycle, it likewise further develops how well the individual alloying components are blended, prompting a superior eventual outcome. When the components are well blended, the end result in expulsion fabrication frequently outperforms.Execution testing showed that parts made of aluminum composites handled with ShAPE surpassed current American Society for Testing and Materials principles for strength and prolongation.
“We investigated using an electron magnifying lens and discovered that ShAPE breaks down the combination totals and disintegrates them into the aluminum lattice before expulsion, making them more extrudable,” said Tianhao Wang, PNNL materials researcher and lead creator on the new publication in Materials and Design.”This means better execution — our aluminum 7075 combinations are more grounded and stretch farther prior to breaking.”
Putting high-performance aluminum alloys in reach
Aluminum composites are esteemed in the auto and aviation industries since they are solid and lightweight. The most elite presentation aluminum composites are significant investments to make, with many business sectors, such as applications in passenger vehicles, valuing them. The ShAPE cycle eliminates a significant obstacle in the development of elite aluminum composites by decisively diminishing energy utilization and ozone depleting substance discharges during assembling.
“This is a significant stage in opening the capability of cutting edge metals assembling to deliver better, less expensive, greener items for what is to come,” said Whalen.
More information: Tianhao Wang et al, Extrusion of Unhomogenized Castings of 7075 Aluminum via ShAPE, Materials & Design (2021). DOI: 10.1016/j.matdes.2021.110374