The innovation, which has been tried in the lab, could at last be utilized for assembling and working in hard-to-get to or risky areas like tall structures or help with post-fiasco alleviation development, say the analysts.
3D printing is picking up speed in the development business. Both on location and in the plant, static and portable robots print materials for use in development projects, like steel and substantial designs.
This novel approach to 3D printing, pioneered by Royal and Empa, the Swiss Government Laboratories of Materials Science and Innovation, employs flying robots, known as robots, that employ aggregate structure strategies inspired by natural developers such as honey bees and wasps that collaborate to create large, complex designs.
“We believe our fleet of drones might assist lower the costs and dangers of building in the future, when compared to existing manual techniques.”
Professor Kovac
The robots in the armada, referred to all in all as Flying Added Substance Assembling (Elevated AM), work co-operatively from a solitary plan, adjusting their methods as they go. They are completely independent while flying yet are observed by a human regulator who looks at progress and mediates if necessary, in view of the data given by the robots.
Lead creator Teacher Kovac, of Royal’s Branch of Flying and Empa’s Materials and Innovation Focus of Advanced Mechanics, said, “We’ve demonstrated that robots can work independently and in pairs to develop and fix structures in the lab. Our answer is versatile and could assist us with developing and fixing work in hard-to-arrive at regions later on.
3D calculation printing
Flying AM utilizes both a 3D printing and way-arranging system to assist the robots with adjusting to variations in the math of the design as the form advances. The armada is comprised of BuilDrones, which store materials during flight, and quality-controlling ScanDrones that constantly measure the BuilDrones’ results and illuminate their next assembling steps.
To test the idea, the analysts created four custom cementitious blends for the robots to work with.
The robots surveyed the printed math continuously and adjusted their ways of behaving to guarantee they met the form details with an assembling precision of five millimeters.
The evidence of idea prints incorporated a 2.05-meter high chamber (72 layers) with a polyurethane-based froth material and an 18-centimeter high chamber (28 layers) with a hand-crafted primary cementitious material.
This innovation offers future opportunities for building and fixing structures in tall or other hard-to-get-to areas. Then, the analysts will work with development organizations to approve the arrangements and give fix and assemble abilities.
Teacher Kovac said, “We accept our armada of robots could assist with lessening the expenses and dangers of development later on, compared with customary manual strategies.”
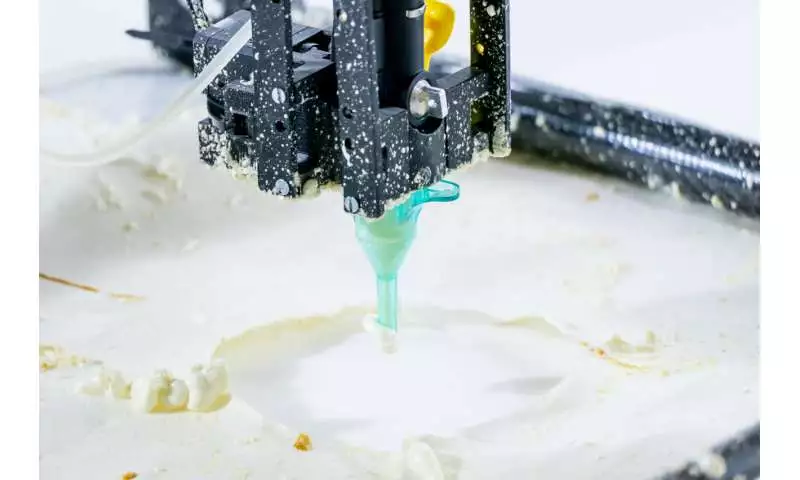
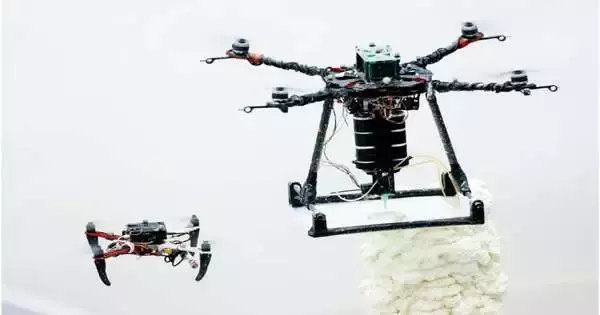

The research is published in Nature.
More information: Mirko Kovac, Aerial additive manufacturing with multiple autonomous robots, Nature (2022). DOI: 10.1038/s41586-022-04988-4. www.nature.com/articles/s41586-022-04988-4
Journal information: Nature