Carnegie Mellon mechanical designing scientists have fostered another versatile and reproducible assembling method that could speed up the standard reception and commercialization of delicate and stretchable gadgets.
The up and coming age of automated innovation will create delicate machines and robots that are protected and agreeable for direct actual connection with people and for use in delicate conditions. Unlike rigid devices, delicate and stretchable hardware can be used to create wearable and implantable devices where safe actual contact with organic tissue and other fragile materials is essential.
Delicate robots that securely handle fragile products of the soil can further develop sanitation by forestalling cross-tainting. Robots produced using delicate materials can overcome the neglected profundities of the ocean to gather fragile marine examples. Also, the numerous biomedical applications for delicate robots incorporate wearable and assistive gadgets, prostheses, delicate apparatuses for medical procedures, drug conveyance gadgets, and fake organ capability.
“In order to address issues that make gallium-based liquid alloys unsuitable for large production, it was necessary to better understand their innate features.”
Kadri Bugra Ozutemiz
Yet, making these almost vague parts that can flawlessly coordinate with human existence is just the initial step. Standard reception and commercialization of delicate and stretchable gadgets will require the improvement of new assembling methods that are adaptable and reproducible.
Although various techniques have previously shown the capacity to create fluid metal-put together gadgets with respect to a more limited size in labs, these strategies have not yet brought about the basic mix of desired highlights expected to deliver fluid metal-based delicate and stretchable hardware at a monetarily feasible scale.

Sans battery RFID, delicate sensor patches are applied to the silicone wafer after creation is finished. Carnegie Mellon University Mechanical Engineering
A group of scientists from Carnegie Mellon University’s College of Engineering looks to change this with a clever strategy they have created for the mass assembling of fluid metal-based delicate and stretchable electronic gadgets. Their work was published in Advanced Materials Technologies.
Kadri Bugra Ozutemiz, who as of late acquired his Ph.D. in mechanical designing, has fostered another methodology that accomplishes versatility, accuracy, and microelectronic similarity by joining the utilization of fluid metal with photolithography and wafer-based plunge covering.
Ozutemiz, who worked with Carmel Majidi and Burak Ozdoganlar, the two teachers of mechanical design, makes sense that fluid metals have become famous lately as a conduit for stretchable circuits to make sensors and radio wires as well as delicate and stretchable wiring for different gadgets and advanced mechanics applications.
The gallium-based amalgam, eutectic gallium-indium (EGaIn), is fluid at room temperature, can openly stream inside channels, has high electrical conductivity, and can be twisted for however long it is embodied in another medium.
“We needed to more readily comprehend the innate properties of gallium-based fluid amalgams to overcome difficulties that make them inadmissible for mass assembling,” said Ozutemiz.
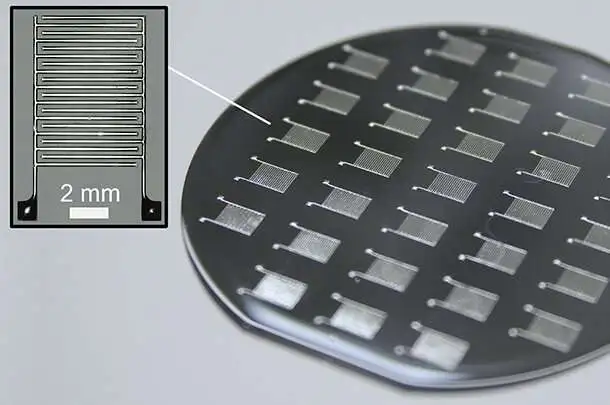
A bunch of 31 delicate brush capacitors are created on the wafer. Mechanical Engineering, Carnegie Mellon University
The main problem was that a slim gallium-oxide “skin” quickly framed when the fluid metal was presented to air, which makes it hard to accomplish a uniform and nonstop shape or math. The fluid metal sticks all over, streaming into a wide assortment of variable shapes.
“Our group conceived a clever methodology that joins specific metal-compound wetting that stores the fluid metal into the ideal circuit format with a plunge covering process that breaks up the oxide skin that results when EGaln is presented to the air,” made sense of Ozutemiz.
Slim metal follows, made of reasonable and promptly accessible copper, are first lithographically designed onto an elastomer surface as a wetting layer. The following act as layouts for specifically saving the EGaln onto the silicone elastic surface.
To break up the oxide skin while keeping up with the specific statement of the fluid metal, the scientists contrived a clever methodology that combined the particular metal-compound wetting with a plunge covering process.
Plunge covering, which has been utilized in the microelectronics business yet not with fluid metals, works with the statement of EGaIn specifically on the circuit format characterized by lithographically designed copper follows on elastomer-covered wafers in a versatile way.
A robotized, high-accuracy movement framework and a two-layer plunging shower are utilized to store the EGaIn onto the designed copper wetting layer. The shower incorporates a slim layer of fluid sodium hydroxide (NaOH) arrangement at the top surface, trailed by the EGaIn. The NaOH arrangement works with the expulsion of oxide skin and of any oxidation on the outer layer of the copper follows when the designed wafer is dunked into the shower. The wafer is then drenched into the shower, and after a short stay time, is removed at a speed that controls how much fluid is kept on the substrate.
The scientists utilized a uniquely incorporated basic machine to dunk the wafers into the shower. By controlling the withdrawal speed, they effectively created repeatable fluid metal calculations.
In future testing, they will attempt to control boundaries like, for example, withdrawal speed and how much time the wafer stays in the shower, to more readily comprehend what influence every variable has on the subsequent math. Yet, for the present, they have laid out a suitable cycle for the large-scale manufacturing of fluid metal circuits that can be utilized in a wide assortment of delicate mechanical and gadget applications.
For our purposes, what was most significant was that we accomplished repeatable outcomes with a standard cycle that is now utilized by chip makers,” said Ozutemiz, who made sense of that by bringing another material into a deep rooted process, makers will actually want to scale creation that will consider more broad reception of these inventive, delicate robots and electronic gadgets.
More information: Kadri Bugra Ozutemiz et al, Scalable Manufacturing of Liquid Metal Circuits, Advanced Materials Technologies (2022). DOI: 10.1002/admt.202200295
Journal information: Advanced Materials Technologies