Electronic gadgets generate heat, which must be dissipated. If not, excessive temperatures can compromise device function or potentially damage the equipment and surroundings. A team has now outlined a new cooling technology that offers a slew of advantages, not the least of which is space efficiency, which gives a significant gain in device power per unit volume over conventional approaches.
The efficiency of an electronic gadget is inversely related to its temperature. A rise in temperature causes a decline in performance. High-performance electronic components generate heat loads that cause high junction temperatures, reduce component lifetimes, and can cause electronic devices to fail prematurely.
Electronic gadgets produce heat, which must be dissipated. If it isn’t, excessive temperatures might impair device performance or possibly cause harm to the devices and their surroundings.
Now, a team from UIUC and UC Berkeley has published an article in Nature Electronics revealing a new cooling method that offers a slew of advantages, not the least of which is space efficiency, which gives a significant increase in device power per unit volume over conventional ways.
In our investigation, we compared our coatings to typical heat sinking methods. What we demonstrated is that the coatings can achieve very similar, if not better, thermal performance than the heat sinks.
Tarek Gebrael
The previous solutions, according to Tarek Gebrael, the primary author and a UIUC Ph.D. student in mechanical engineering, have three flaws. “For starters, they can be costly and difficult to scale up,” he explains. Diamond heat spreaders, for example, are occasionally utilized at the chip level, but they are not cheap.
Second, traditional heat spreading systems often require that the heat spreader and a heat sink – a device for efficiently dispersing heat, toward which the spreader directs the heat – be attached to the top of the electronic device. Unfortunately, “in many circumstances, the majority of the heat is created beneath the electrical equipment,” implying that the cooling system isn’t performing optimally.
Third, cutting-edge heat spreaders cannot be put directly on the surface of the electronics; instead, a layer of “thermal interface material” must be layered between them to ensure proper contact. That middle layer, however, has a negative impact on thermal performance due to its weak heat transmission characteristics.
The new solution addresses all three of those problems.
To begin, the primary material used is copper, which is a reasonably inexpensive material. Second, according to Gebrael, the copper coating completely “engulfs” the device, “covering the top, bottom, and sides… a conformal coating that covers all the exposed surfaces,” ensuring that no heat-producing zones are overlooked. Third, no thermal interface material is required because the device and copper heat spreader are practically one item. There is also no requirement for a heat sink.
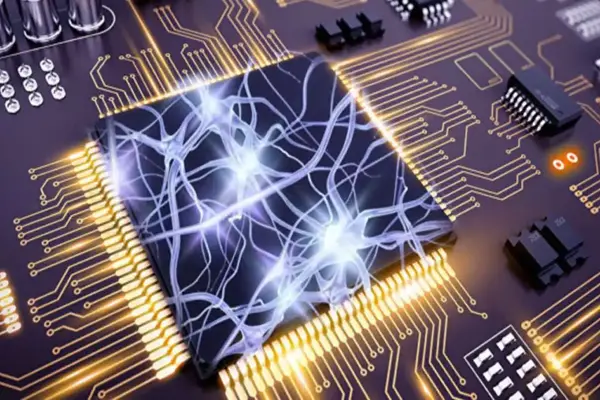
“In our investigation, we compared our coatings to typical heat sinking methods,” Gebrael explains. “What we demonstrated is that the coatings can achieve very similar, if not better, thermal performance than the heat sinks.” Nonetheless, a gadget using the new method is far smaller than one using heat sinks, which are hefty. “As a result, the power per unit volume is substantially higher. We were able to show a 740 percent improvement in power per unit “volume.”
That makes a huge difference in the real world. “Let’s say you have multiple printed circuit boards,” says Gebrael. “You can stack many more printed circuit boards in the same volume when you are using our coating, compared to if you are using conventional liquid- or air-cooled heat sinks.”
Co-author Nenad Miljkovic, an associate professor of mechanical science and engineering at UIUC and Gebrael’s advisor, explains, “This technique connects two distinct thermal management approaches: near-junction device-level cooling and board-level heat spreading. Tarek’s work in partnership with the team at UC Berkeley has enabled us to employ a non-siloed electro-thermo-mechanical technology development method to provide a solution to a difficult challenge for numerous industries.”
Miljkovic said the team is continuing to expand the work, which is partially sponsored by ARPA-E and the POETS NSF ERC at UIUC.
They are still exploring the coatings’ dependability and durability, which are important to industrial adoption. The article already demonstrated that the coatings may be employed in both air and water, the latter of which is required for “immersion cooling” applications. The team is now investigating dependability in boiling water, boiling dielectric fluids, and high-voltage settings. They will also apply the coatings to full-scale power modules and GPU cards, as opposed to basic test boards in the initial effort.
Those continued efforts should bring the novel technology one step closer to industrial and commercial production for a number of applications such as power electronics cooling, data center thermal management, and electric machine cooling.