A strain-detecting savvy skin created at Rice University that utilizes tiny designs, carbon nanotubes, to screen and identify harm in huge designs is good to go.
Rice discovered the “strain paint” a long time ago, using the fluorescent properties of nanotubes to show when a surface has been twisted by pressure.
The complex covering can be applied to large surfaces, such as spans, structures, boats, and planes, where high strain poses an undetectable risk.
The task driven by Rice scientist Bruce Weisman, primary designer Satish Nagarajaiah and lead creator and graduate understudy Wei Meng springs from the 2002 revelation by Weisman that semiconducting carbon nanotubes fluoresce at close infrared frequencies. He thusly created optical instruments to investigate the physical and compound properties of nanotubes, including spectroscopic strain impacts, in 2008.
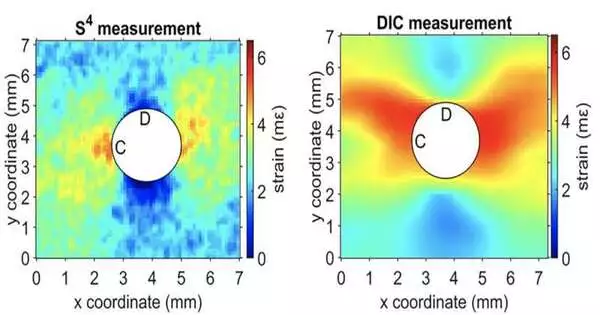
An examination of estimations on an acrylic under strain shows Rice University’s S4 framework, left, gives a more definite readout than the standard computerized picture connection (DIC), at right. Credit: Nagarajaiah and Weisman Research Groups/Rice University
In 2004, Nagarajaiah proposed and fostered a non-contact optical strain sensor utilizing carbon nanotube films clung to primary individuals with epoxy and tested with Raman spectroscopy.
Their free exploration ways converged into a typical task in 2008 when Weisman and Nagarajaiah found that solitary-walled carbon nanotubes implanted in a polymer and clung to a primary part will encounter a similar strain and can report it optically through ghostly changes in their close-infrared fluorescence. They detailed that tracking in a 2012 paper.
“Strain estimations are frequently made as a feature of security-related reviews,” Weisman said. “That specialized local area is legitimately moderate, on the grounds that their estimations should be solid. So we want to beat doubt about new techniques by demonstrating that our own are basically as legitimate as the laid out ones.
“This paper presents our strategy’s qualifications as a serious strain estimation innovation,” he said.
Subtleties of the future, non-contact framework show up in Scientific Reports.
Strain planning has depended on two advances: actual checks joined to structures; and computerized picture connection (DIC), used to look at pictures, assumes control over the long run of surfaces with inserted “dots.”
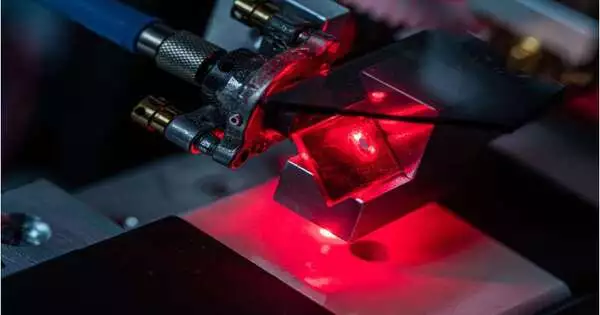
A Rice University lab tests material shrouded in strain-detecting savvy skin. The multi-facet covering contains carbon nanotubes that fluoresce when under strain, matching the strain experienced by the material under. Credit: Jeff Fitlow/Rice University.
Weisman said S4 effectively faces DIC. Even better, the two methods can cooperate. “We needed to make an immediate correlation with DIC, which is the main marketing outlining strategy for strains there,” he said. “It’s utilized in various ventures, and individuals have a genuinely elevated degree of trust in it.”
“To show the way that our strategy can work side by side with it and obtain results that are comparable or better, Wei conceived a strategy to integrate S4 and DIC so the two methods can be utilized all the while and even complete one another,” Weisman said.
The actual skin has three layers, their setup equipped for the surface they cover. Normally, a dark ground containing the DIC dots is painted first. The subsequent layer is a reasonable polyurethane that detaches the base from the nanotubes. At last, the detection layer of separately covered nanotubes, suspended in toluene, is showered on top. The toluene vanishes, leaving a sub-micron-thick detecting layer of nanotubes clinging to the primary part. An extra defensive layer can be applied on top to save the skin dynamic for quite a long time.
The framework likewise requires a peruser, for this situation a little noticeable laser to energize the nanotubes and a compact spectrometer to perceive how they’re stressed.
Meng painstakingly contrasted S4 with both DIC and virtual experiences in tests on I-molded acrylic bars with an opening or a pattern, and on substantial blocks and aluminum plates with openings bored into them to concentrate strain designs. For each situation, S4 gave a high-goal, exact perspective on the situation and focused on examples that were similar to or better than the concurrent DIC results.
Estimating concrete represented an optical test. “We found that concrete in the substantial has natural close-infrared outflow that was impeding our strain estimations,” Nagarajaiah said. “Wei invested a huge measure of energy, particularly during the pandemic, cautiously dealing with another design to hinder those signs.”
Instead of the typical white base layer, a dark base that likewise holds the dots filled the need, he said.
“There’s one extra benefit of S4 over DIC that we hadn’t appreciated up to this point,” Weisman said. “That is the way that to obtain great outcomes from DIC requires an elevated degree of skill with respect to the administrator.” Organizations let us know that their designers are able to utilize it. It’s easy to take the information, yet the translation requires a ton of judgment.
“Our strategy is very unique,” he said. “It’s close to as simple as taking the information, yet the examination to get the S4 strain map is programmed.” Over the long haul, that will be a benefit. “
“I have presumably that this is a cutting-edge strain-planning strategy,” Nagarajaiah said. “We’ve tried it on primary individuals made of metals, plastics, and cement with complex miniature breaks and subsurface harm, and it works in all cases.” I accept we’ve arrived at the stage where it’s prepared for execution, and we are drawing in with industry to figure out how it can help them. “
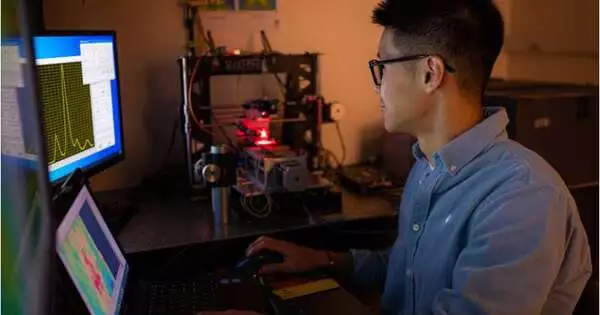
Graduate understudy Wei Meng works at a test rig at a Rice University lab, approving estimations of strain in various materials with strain-detecting savvy skin. Credit: Jeff Fitlow/Rice University.
Rice research researcher Sergei Bachilo and graduate understudy Ashish Pal are co-creators of the review. Weisman is a teacher of science and of materials science and nanoengineering. Nagarajaiah is a teacher of common and natural design, materials science and nanoengineering, and mechanical design.
More information: Wei Meng et al, Next-generation 2D optical strain mapping with strain-sensing smart skin compared to digital image correlation, Scientific Reports (2022). DOI: 10.1038/s41598-022-15332-1