A coating developed by researchers at the Department of Energy’s Oak Ridge National Laboratory has the potential to significantly reduce friction in common load-bearing systems with moving parts, such as wind and hydroelectric turbines and vehicle drive trains. It reduces the amount of friction between steel and steel by at least one hundred times. The novel ORNL coating has the potential to help lubricate a U.S. economy that annually loses more than $1 trillion to wear and friction, or 5% of GDP.
Jun Qu, who is in charge of ORNL’s Surface Engineering and Tribology team, stated, “There is friction and wear when components are sliding past each other.” The science and technology of interacting surfaces in relative motion, such as gears and bearings, is called tribology, from the Greek word for “rubbing.” Assuming that we decrease contact, we can diminish energy utilization. We can extend the system’s lifespan for improved reliability and durability if we reduce wear.”
“Our main achievement is that we make super lubricity feasible for the most common applications, Previously, it was only seen at the nanoscale or in specialized environments.”
Jun Qu, leader of ORNL’s Surface Engineering and Tribology group.
Qu led a study about a coating made of carbon nanotubes that gives sliding parts superlubricity and was published in Materials Today Nano along with ORNL colleagues Chanaka Kumara and Michael Lance. Superlubricity is the ability to exhibit virtually no sliding resistance; a friction coefficient of less than 0.01 is its hallmark. In correlation, when dry metals slide past one another, the coefficient of rubbing is around 0.5. The coefficient of friction drops to about 0.1 when using an oil lubricant. However, the ORNL coating decreased the coefficient of friction to as low as 0.001, well below the superlubricity threshold.
“Our primary accomplishment is that we make superlubricity achievable for the most widely recognized applications,” Qu said. “In the past, it was only seen in special environments or at the nanoscale.”
Kumara grew carbon nanotubes on steel plates for the study. He and Qu used a device known as a tribometer to make the plates rub against each other to produce carbon nanotube shavings.
The multiwalled carbon nanotubes protect the steel from corrosive moisture and serve as a reservoir for lubricant. At the point when they are first stored, the inwardly adjusted carbon nanotubes stand on a superficial level like pieces of turf. At the point when steel parts slide past one another, they basically “cut the grass.” The rolled graphene, an atomically thin sheet of carbon arranged in adjacent hexagons like chicken wire, makes up multiple layers of each hollow blade. The shaving debris of fractured carbon nanotubes is redeposited onto the contact surface, forming a graphene-rich tribofilm that virtually eliminates friction.
The production of carbon nanotubes involves multiple steps. To start with, we really want to actuate the steel surface to deliver minuscule designs on the scale of nanometers. Second, we want to provide a carbon source to develop the carbon nanotubes,” Kumara said. He heated a disk made of stainless steel to produce metal oxide on its surface. After that, he introduced carbon in the form of ethanol through chemical vapor deposition, enabling metal-oxide particles to atom-by-atom join carbon to form nanotubes there.
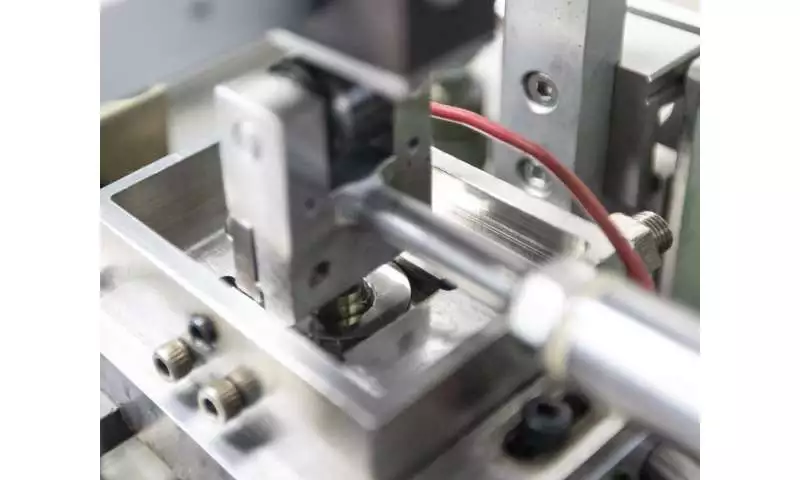
Credit: Carlos Jones/ORNL, U.S. Dept. of Energy
The new nanotubes don’t give superlubricity until they are harmed.” Qu stated, “The rubbing destroys the carbon nanotubes but creates new ones.” The key part is that those broken carbon nanotubes are bits of graphene. During the process, those graphene fragments are smeared and connected to the contact area to form tribofilm, a coating. After that, a coating containing graphene is applied to both of the contact surfaces. Now, when they rub, it looks like graphene on graphene.”
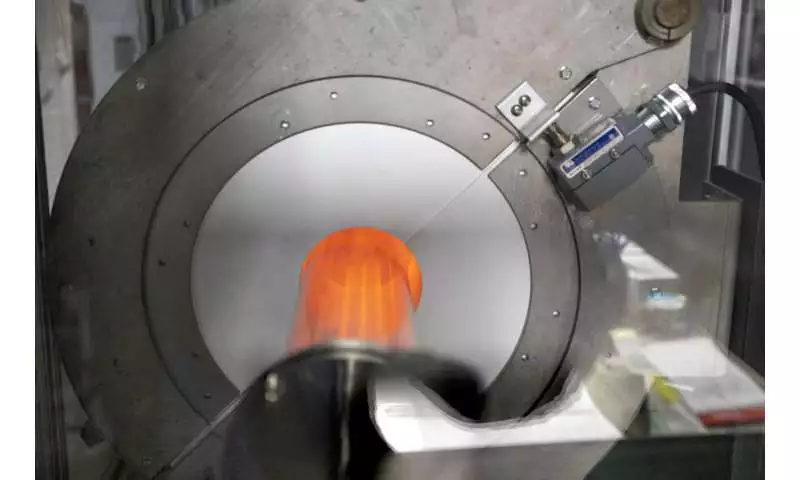
Credit: Carlos Jones/ORNL, U.S. Dept. of Energy
To achieve superlubricity, even a single drop of oil is required. We gave it a shot without oil.” Qu said it didn’t work. “The reason for this is that when there is no oil, friction removes the carbon nanotubes too quickly. Then the tribofilm can’t shape pleasantly or endure long. It’s like not having oil in an engine. It smokes shortly, while one with oil can undoubtedly run for a really long time.”
The ORNL’s prevalent trickiness has fortitude. Superlubricity continued in a trial of in excess of 500,000 scouring cycles. Kumara evaluated the performances for continuous sliding for a period of three hours, one day, and then twelve days. We actually have superlubricity,” he said. “It is steady.
Utilizing electron microscopy, Kumara analyzed the cut pieces to demonstrate that tribological wear had cut off the carbon nanotubes. ORNL co-author Lance utilized Raman spectroscopy, a method that measures vibrational energy related to a material’s atomic bonding and crystal structure, to independently confirm that rubbing had shortened the nanotubes.
Qu stated, “Modern science and engineering provided a new scientific approach to advance technology in this area, although tribology is a very old field.” The major comprehension has been shallow until the last perhaps 20 years, when tribology got another life. Utilizing the more cutting-edge technologies for material characterization, scientists and engineers have recently really collaborated—an ORNL strength. Tribology is very intertwined. Nobody is an expert in all areas. Accordingly, in tribology, the way to progress is joint effort.”
He added, “Somewhere, you can track down a researcher with skill in carbon nanotubes, a researcher with mastery in tribology, or a researcher with skill in material portrayal. Yet they are disengaged. Around here at ORNL, we are together.”
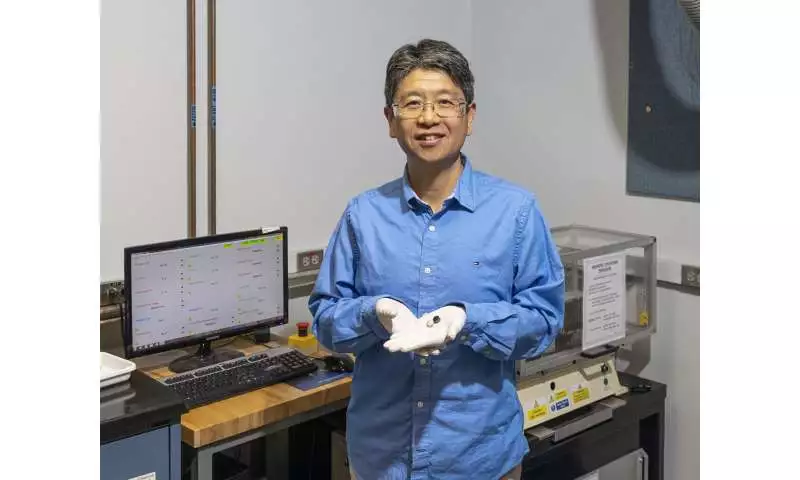
Jun Qu of ORNL shows stainless-steel disks before (silver) and after (black) coating with carbon nanotubes that provide superlubricity. Credit: Carlos Jones/ORNL, U.S. Dept. of Energy
ORNL’s tribology groups have accomplished grant-winning work that has drawn in modern organizations and authors. An R&D 100 award was presented in 2014 to an ionic anti-wear additive developed by ORNL, General Motors, Shell Global Solutions, and Lubrizol for fuel-efficient engine lubricants. Qu, Huimin Luo, Sheng Dai, Peter Blau, Todd Toops, Brian West, and Bruce Bunting were the ORNL collaborators.
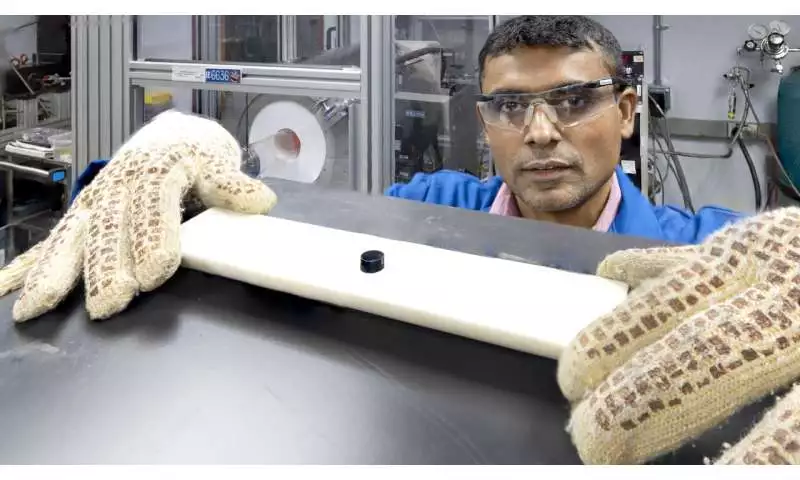
Chanaka Kumara of ORNL used a chemical vapor deposition system, in the background, to coat a stainless-steel disc, in the foreground, with carbon nanotubes. Credit: Carlos Jones/ORNL, U.S. Dept. of Energy
In a similar vein, the work that is the subject of this paper was one of the finalists for the R&D 100 award in 2020. Their novel superlubricity coating has been the subject of a patent application by the researchers.
“Then, we desire to collaborate with industry to compose a joint proposition to DOE to test, mature, and permit innovation,” Qu said. “In 10 years, we might want to see work on superior execution vehicles and power plants with less energy lost to grating and wear.”
More information: Chanaka Kumara et al, Macroscale superlubricity by a sacrificial carbon nanotube coating, Materials Today Nano (2022). DOI: 10.1016/j.mtnano.2022.100297