Bioreactors are vessels or tanks in which entire cells or cell-free enzymes convert raw materials into biochemical products and/or less undesired byproducts. The microbial cell is a tiny bioreactor; other examples include shaking flasks, Petri plates, and industrial fermentors. Diagnostic products based on enzymatic reactions, agricultural silos for silage fermentation, bread pans with fermenting yeast, and the soil of a Kansas wheat field can all be considered bioreactors.
The School of Biosciences at the University of Kent has designed and manufactured equipment that can be used to research bacterial biofuel generation at a quarter of the cost of commercial systems. This approach was then utilized to show how bacterial genetic engineering could be applied to improve biofuel production.
Commercial equipment used to investigate biofuel-producing bacteria can be prohibitively expensive, so the team decided to create their own bioreactors, which are available to most research institutes. The researchers then utilized this technology to confirm that one of their genetically altered Clostridium bacterium strains could generate butanol more quickly.
These exciting developments will help to advance research into bacterial biofuel production, and we are especially excited to use our expertise to optimize processes that can convert waste products from food and agriculture into biofuels that are greener alternatives to fossil fuels.
Dr Mark Shepherd
A bioreactor is the core of biological processes. The biological systems involved include enzymes, microorganisms, animal cells, plant cells, and tissues. To design an appropriate bioreactor for a particular bioprocess, intensive studies on the biological system, such as cell growth, metabolism, genetic manipulation, and protein or other product expressions, are needed to understand the cells’ requirements in their physical and chemical environment. It is also necessary to control and optimize the bioreactor environment via operating variables in order to favor the desired functions of the cells and achieve cost-effective large-scale manufacture.
Bioreactor systems are a vital component in the process of 3D tissue engineering and the formation of tissue constructs. Bioreactors are used to provide a tissue-specific physiological in vitro environment during tissue maturation. Based on the bioreactor technology, various tissue systems can be incubated in vitro.
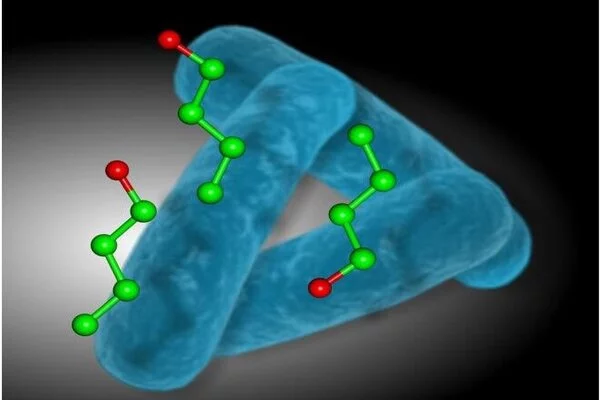
These research findings, which have been published in the journals Access Microbiology and Microbial Biotechnology, reveal that a subtle change to a single gene can result in remarkable changes to how sugars are converted to biofuel products. It is expected that this work will improve accessibility to cheaper bioreactors to stimulate wider research into biofuel production using natural and engineered bacteria.
Corresponding author Dr Mark Shepherd, Senior Lecturer in Microbial Chemistry at Kent, stated, ‘These exciting developments will help to advance research into bacterial biofuel production, and we are especially excited to use our expertise to optimize processes that can convert waste products from food and agriculture into biofuels that are greener alternatives to fossil fuels.’
The study’s findings were reported in Access Microbiology and Microbial Biotechnology. The findings show that a small change in a single gene can result in dramatic changes in the way carbohydrates are transformed into biofuel products.
Researchers anticipate that better availability to inexpensive bioreactors will promote additional study into biofuel production using natural origin laboratory-generated bacteria as a result of the finding. These intriguing results will aid in the advancement of bacterial biofuel research. According to the study’s accompanying author, it is especially fascinating to employ self-expertise to enhance procedures that can convert waste from food and agriculture into biofuels that are cleaner alternatives to fossil fuels.