Traditional assembling techniques, for example, delicate lithography and hot embellishing cycles, can be utilized to bioengineer microfluidic chips, but with constraints, including trouble getting diverse designs, cost- and work-consuming creation processes, and low efficiency.
Materials researchers have presented computerized light handling as a savvy microfabrication way to deal with 3D printed microfluidic chips, although the creation goal of these microchannels is restricted to a size of sub-100 microns.
In another report distributed in Microsystems and Nanoengineering, Zhuming Luo and a logical group in biomedical design and synthetic design in China fostered an imaginative computerized light handling technique.
They proposed a changed numerical model to foresee UV irradiance for gum photopolymerization and directed the manufacture of microchannels with an expanded goal. The high-level microfabrication strategy can work with significant improvements in exact and versatile microchannel development as a critical next stage for broad applications in microfluidics-based systems in biomedicine.
Microfluidic chips
The microfluidics chips offer a useful asset to scale down applications in 3D cell culture for drug screening and testing applications and organ-on-a-chip measures. Regular techniques to create microfluidic chips incorporate delicate lithography and hot-fine manufacturing with confounded design interactions, low efficiency, and significant expense.
3D bioprinting has drawn in an expanding regard for imaginatively planning and assembling tweaked structures at the microscale. Materials researchers have used computerized light handling for layer-by-layer tank photopolymerization to microfabricate with goals up to many microns with a quick handling rate and simplicity of capability.
In this work, Luo and partners fostered another advanced light handling strategy for high-goal and scale-up creation of microfluidic gadgets by dosing and drafting tank polymerization. The group adjusted the printing boundaries and different boundaries to unequivocally tailor the photopolymerization of adjoining pitch layers and keep away from channel obstruction because of unreasonable UV openness.
When contrasted with ordinary strategies, the cycle permitted the one-bunch improvement of up to 16 microfluidic chips. The ongoing technique can work with significant advances in exact and versatile microchannel improvement as a critical forward-moving step for microfluidics-based gadgets in biomedicine.
Utilizing a numerical model to foresee the trademark boundaries of sap
The group controlled the UV light measurements by applying stepwise UV to polymerize the sap layer by layer using a numerical model. Upon UV illumination for a particular openness time, the researchers polymerized a particular depth of the pitch arrangement. Then, utilizing the numerical model, they decided on a far-reaching technique to work out the limit of gum polymerization. The printing method integrated into the work unequivocally isolated the microchannel into the base layer, channel layer, and rooftop layer.
Plan reasoning and exploratory arrangements for microchannel improvement.
In view of the results, the scientists proposed a modified rendition of the computerized light cycle (DLP) printing system to manufacture significantly smaller micro channels through dosing-and-drafting controlled tank photopolymerization (contracted DZC-VPP). This interaction isolated the micro channels into a few layers. The ability to manage the zones for every projection step permitted the exact guidelines of neighborhood pitch polymerization, and the researchers effectively printed the channels with a fundamentally higher goal.
The group concentrated on the printing nature of the new methodology by contrasting it with the regular technique. While the customary strategy prompted unfortunate channel loyalty because of the gathering of inordinate UV openness, the new technique contrastingly offered micro channels with fundamentally further developed printing constancy to permit the improvement of smoother inside surfaces inside the micro channels, with a huge effect on fluid control. The DZC-VPP strategy is also profoundly versatile and savvy.
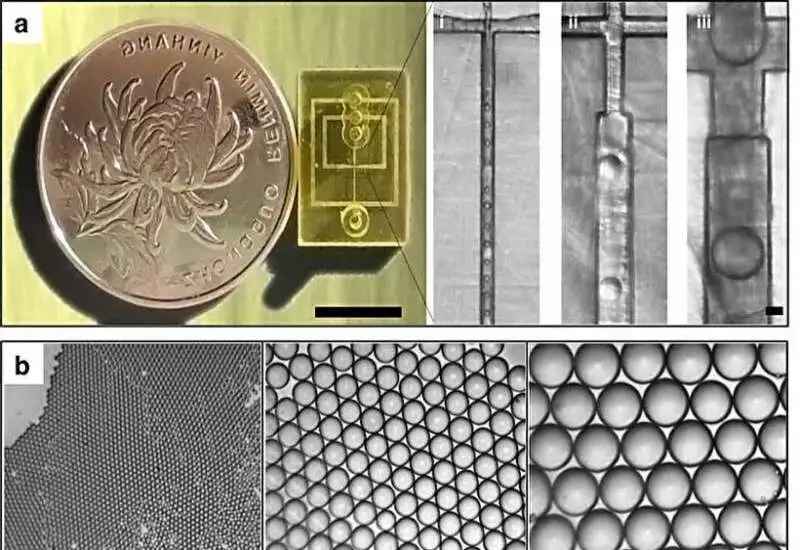
Exploratory information on DZC-VPP chips for the re-creation of microdroplets and microgels a) The photo shows the volume of a solitary DZC-VPP chip in contrast with the coin, and the magnifying lens pictures show stream designs produced in the microfluidic gadget at various channel sizes of 20 μm (I), 100 μm (ii), and 300 μm (iii). Scale bars are 1 cm in photos and 100 μm in magnifying lens pictures. b) Delegate magnifying lens pictures of microdroplets created by DZC-VPP chips with channel sizes of 20 μm (I), 100 μm (ii), and 300 μm (iii). Scale bars are 300 μm. c) Agent confocal minute pictures of microgels produced by DZC-VPP chips with channel sizes of 20 μm (I), 100 μm (ii), and 300 μm (iii). Scale bars are 300 μm. d) Size appropriation of microdroplets and microgels produced by DZC-VPP chips (five chips for each example) with channel sizes of 20 μm (I), 100 μm (ii), and 300 μm (iii). Credit: Microsystems and Nanoengineering (2023). DOI: 10.1038/s41378-023-00542-y
Mechanical solidity of the created materials.
Luo and partners next researched the mechanical security of the microfluidic gadgets designed with the new DZC-VPP strategy and again contrasted it with the regular cycle. While mechanical security is vital for the microfluidic chips to endure high fluid tension, the two materials exhibited comparable pressure strain bends.
The DZC-VPP-manufactured chip showed fundamentally higher break anxiety when contrasted with the DLP chip, demonstrating that the new system further developed both the printing goal and the mechanical security of the designed microfluidic chips.
Creating drops and microgels and epitomizing cells with microgels
To achieve a microfluidic age of beads, the researchers used unadulterated water as the fluid stage and an oil-glycol emulsion to make monodisperse fluid drops. The group epitomized the cells with microgels in the chips by utilizing the alginate framework. To prevent cytotoxicity in the instrument, the specialists tested the biocompatibility of the chips utilizing cell-loaded microgels.
Both HeLa cells and rodent mesenchymal cells utilized in the review held cell suitability after exemplification to steadily multiply into cell groups, demonstrating the biofriendly idea of the DZC-VPP-designed microfluidic gadget. The technique is likewise ideal for other cell-related applications, remembering the improvement of organ-for-a-chip instruments.
When contrasted with the traditional advanced light printing process, the fresher DC-VPP strategy can manage the UV infiltration depth for gum photopolymerization. The results featured the unwavering quality of the new cycle for high-goal printing to manufacture 3D-printed microfluidic chips.
Viewpoint
Along these lines, Zhuming Luo and the exploration group fostered a new dosing and drafting strategy for managed tank photopolymerization (condensed DZC-VPP) to 3D print micro channels with further developed goals and mechanical solidity. The group achieved this by proposing a numerical model to anticipate the gathered UV irradiance for tar polymerization as a manual for planning and printing the micro channels.
Utilizing the methodology, the group printed a microchannel with regular delicate lithography or hot emblazoning to create high-throughput monodisperse beads and cell-loaded microgels. This exceptionally proficient strategy for microfabrication addresses a vital stage for the high-goal, increased creation of microfluidic gadgets for inescapable applications.
More information: Zhiming Luo et al, Digital light processing 3D printing for microfluidic chips with enhanced resolution via dosing- and zoning-controlled vat photopolymerization, Microsystems & Nanoengineering (2023). DOI: 10.1038/s41378-023-00542-y