Scientists at Chalmers College of Innovation, Sweden, have tracked down a new and productive method for reusing metals from spent electric vehicle batteries. The technique permits the recuperation of 100 percent of the aluminum and 98% of the lithium in electric vehicle batteries. Simultaneously, the deficiency of important unrefined components, for example, nickel, cobalt, and manganese, is limited. No costly or hurtful synthetic substances are expected in the process in light of the fact that the scientists use oxalic corrosive, a natural corrosive that can be tracked down in the plant realm.
The article “Complete and particular recuperation of lithium from EV lithium-particle batteries: Displaying and streamlining utilizing oxalic corrosive as a filtering specialist” was distributed in the diary Division and Purging Innovation.
“Up to this point, nobody has figured out how to track down precisely the perfect circumstances for isolating this much lithium using oxalic corrosive while additionally eliminating all the aluminum. Since all batteries contain aluminum, we should have the option to eliminate it without losing different metals,” says Léa Rouquette, Ph.D. understudy at the Division of Science and Compound Designing at Chalmers.
“No one has yet found the exact conditions for separating this much lithium using oxalic acid while also removing all of the aluminum. Because all batteries include aluminum, we must be able to extract it without contaminating the other metals.”
Léa Rouquette, Ph.D. student at the Department of Chemistry and Chemical Engineering at Chalmers.
In Chalmers’ battery reuse lab, Rouquette and research pioneer Martina Petranikova show how the new technique functions. The lab has spent vehicle battery cells and, in the smoke cabinet, their pounded contents. This appears to be a finely ground dark powder that broke up in a straightforward fluid—oxalic corrosive.
Show the new and productive technique for reusing metals from electric vehicle batteries. Léa Rouquette makes sense of the cycle in the lab at Chalmers College of Innovation, Sweden. Credit: Chalmers College of Innovation, Mia Halleröd
Rouquette produces both the powder and the fluid in something suggestive of a kitchen blender. In spite of the fact that it looks as simple as blending espresso, the specific methodology is novel and, as of late, a logical leap forward. By tweaking the temperature, fixation, and time, the specialists have concocted a wonderful new recipe for utilizing oxalic corrosive—a harmless to the ecosystem fixing that can be found in plants like rhubarb and spinach.
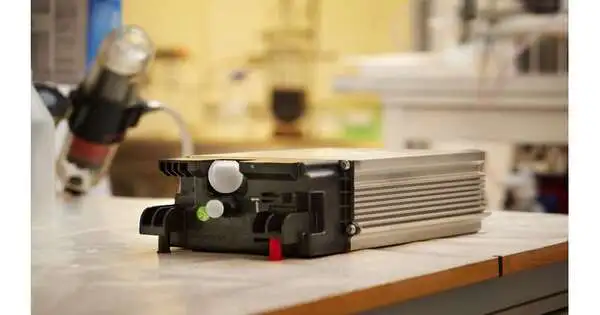
The researchers at Chalmers work with real spent car batteries from Volvo Cars. Here is a battery module, holding 14 battery cells. Credit: Chalmers University of Technology | Anna-Lena Lundqvist
“We really want options in contrast to inorganic synthetics. Perhaps the greatest bottleneck in the present cycle is eliminating remaining materials like aluminum. This is a creative technique that can offer the reusing business new other options and assist with tackling issues that thwart improvement,” says Martina Petranikova, academic partner at the Division of Science and Synthetic Design at Chalmers.
Turning around requests and keeping away from the misfortune
The water-based reusing strategy is called hydrometallurgy. In conventional hydrometallurgy, every one of the metals in an EV battery cell is broken up in an inorganic corrosive. Then, you eliminate the “pollutions” like aluminum and copper. Finally, you can independently recover significant metals like cobalt, nickel, manganese, and lithium.
Despite the fact that the amount of leftover aluminum and copper is small, it requires a few sanitization steps, and each move toward this cycle can cause lithium misfortune. With the new strategy, the scientists invert the request and recuperate the lithium and aluminum first. Hence, they can diminish the misuse of significant metals expected to make new batteries.
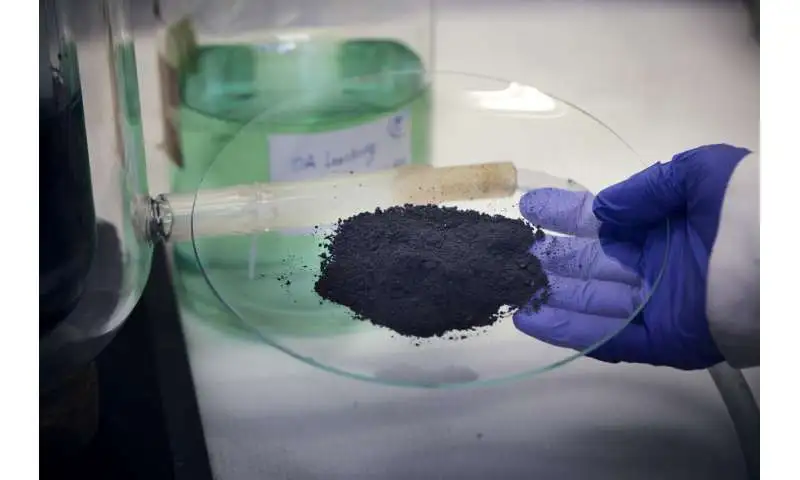
After the aqueous-based recycling method, the aluminum and lithium end up in the (greenish blue) liquid. The other metals, such as cobalt, nickel and manganese, remain in the dark “solids”, shown on the plate. Credit: Chalmers University of Technology | Anna-Lena Lundqvist
The last option part of the cycle, in which the dark blend is separated, is likewise suggestive of preparing espresso. While aluminum and lithium end up in the fluid, different metals are left in the “solids.” The subsequent stage in the process is to isolate aluminum and lithium.
“Since the metals have altogether different properties, we don’t think it’ll be difficult to isolate them. Our technique is a promising new course for battery reusing—a course that certainly warrants further investigation,” says Rouquette. “As the technique can be increased, we trust it will be utilized in industry in the years to come,” says Petranikova.
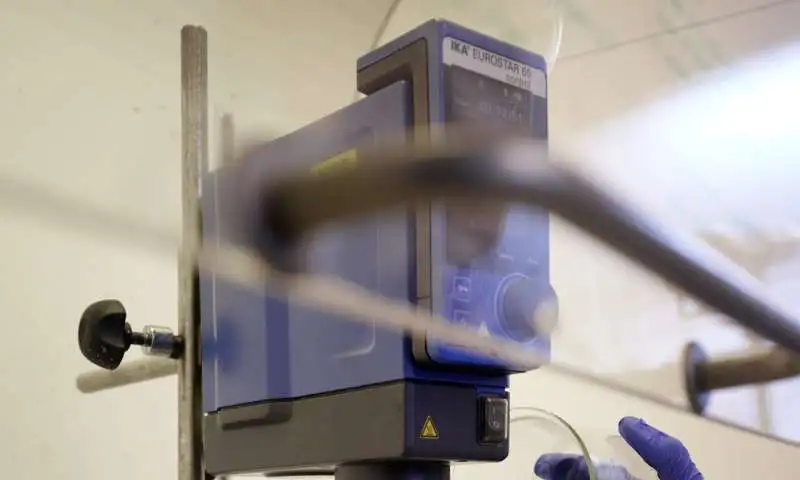
The finely ground contents of a car battery cell are added to and dissolved in oxalic acid. By fine-tuning the temperature, concentration and time, the researchers have come up with an excellent new recipe for using oxalic acid – an environmentally friendly reactant ingredient found in plants such as rhubarb and spinach. Credit: Chalmers University of Technology | Anna-Lena Lundqvist
Petranikova’s examination bunch has gone through numerous years of state-of-the-art research in the reusing of metals tracked down in lithium-particle batteries. The gathering is engaged in different joint efforts with organizations to foster electric vehicle battery reuse and is an accomplice in significant innovative work projects, for example, Volvo Vehicles’ and Northvolt’s Nybat project.
The review was directed by Léa Rouquette, Martina Petranikova, and Nathália Vieceli at the Branch of Science and Synthetic Designing at Chalmers College of Innovation, Sweden.
More information: Léa M.J. Rouquette et al, Complete and selective recovery of lithium from EV lithium-ion batteries: Modeling and optimization using oxalic acid as a leaching agent, Separation and Purification Technology (2023). DOI: 10.1016/j.seppur.2023.124143