As interest in new energy sources develops, the wastewater co-delivered close by oil and gas (created water) indicates that things are not pulling back: The flow volume of wastewater—the aftereffect of water constrained underground to crack stone and deliver the stores—is assessed at 250 million barrels each day, compared with 80 million barrels per day of oil.
Engineers at the University of Pittsburgh Swanson School of Engineering are developing a better method to reduce the environmental impact of deep and penetrating oil drilling by cleaning the delivered water for reuse, which is currently being tested in Pennsylvania, Texas, and North Dakota.
Layer refining is an emerging innovation that can treat complex and exceptionally defiled wastewater. This task, driven by Radisav Vidic, teacher and chair of the Department of Civil and Environmental Engineering, utilizes layer refining innovation that empowers drillers to channel and reuse the created water in the oil and gas industry, in agribusiness, and for other helpful purposes.
“It is of basic significance to foster elective methodologies for the administration of delivered water that would lessen the general expense, permit recuperation of important assets, and diminish the natural impression of this industry,” said Vidic. “At this moment, business isn’t being given monetarily practical choices. This undertaking demonstrates that those choices would be able to and do exist. “
Delivered water contains numerous contaminants that prevent it from being treated in civil offices: it is several times saltier than seawater and contains microbes, sand, mud, oil, and oil, as well as naturally occurring radioactive materials.Ebb and flow the executives’ procedures for creating water, incorporating infusions into removal wells; handling to recuperate additional oil from the water; and helpful reuse after treatment.
Infusion into a removal well is the most economical choice — and in this way, the most widely recognized — yet it prompts a long-lasting loss of water from the environment. While dry spells are less of an issue in Pennsylvania than in other parts of the country where penetration is common, delivered water that isn’t reused for pressure driven breaking is moved to Ohio for removal, adding to the environmental concern of fuel use and discharges in transport as well as cost.
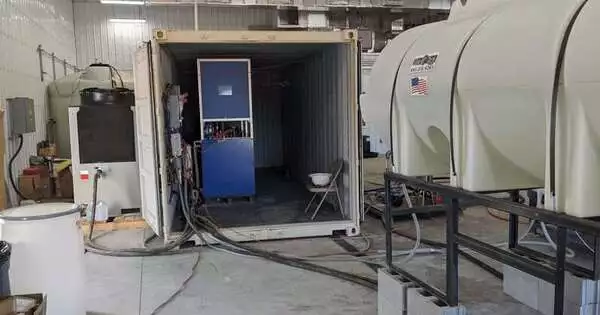
Credit: University of Pittsburgh
Making a closed framework: Treating wastewater with squander heat
As Vidic’s gathering attempted to increase the innovation with the goal that the work means the field, Vikas Khanna, academic administrator of common and ecological designing at Pitt and Wellington C. Carl Faculty Fellow, utilized displaying to imagine what these frameworks would resemble at scale and what the monetary advantage would truly be in the event that the business embraced the innovation.
“Something we found was that on the off chance that you can’t deal with this water in regions like Pennsylvania without infusion wells, you need to truck this water elsewhere to discard it,” said Khanna. “It costs cash to treat the water, yet when you contrast it with the’same old thing’ choice, that is the point at which you begin to see the advantages.”
The proposed arrangement utilizes squander intensity to meet the innovation’s nuclear power prerequisites, further diminishing the activity costs. Northeastern districts in the state—those farthest from removal wells—stand to benefit the most from utilizing this innovation, saving almost $16 million every year in removal costs.
From the lab to the field
The undertaking started in the lab around a long time back and was first brought into the field for pilot-scale testing, with subsidies from the U.S. Branch of Energy, in Texas and North Dakota oilfields. The gathering has now started executing a similar innovation in Pennsylvania’s Marcellus Shale penetrating nearby in New Stanton, Pa.
A pilot-scale film refining framework was set up at a Marcellus Shale penetrating office in Pennsylvania. University of Pittsburgh is to blame.
Various scientists have invested energy attempting to carry this innovation to the field, but the ongoing group incorporates Ph.D. up-and-comers Ritesh Pawar and Zhewei (Joey) Zhang.
“We were both dealing with layer refining (MD) for quite a long time before this on-location project.” “In the lab, MD simply implies research points and trials,” said Zhang. “However, it wasn’t until we started this task with a pilot scale unit and a genuine deep-earth drilling site that we realized how much this innovation could mean for human culture and the climate.”
However, while executing the innovation in Marcellus Shale wells, the group experienced an issue: the administrators added surfactants into their wells to upgrade the well’s efficiency and diminish energy utilization. The surfactants will cause wetting of the layer, which will fall apart the nature of the recuperated water. The group is back in the lab to track down a fix.
“We are taking a gander at treatment choices to eliminate surfactants preceding layer refining and have had some outcomes in the lab with enacted carbon adsorption,” said Vidic. “While we haven’t yet carried out this strategy in the field, we have confirmed our outcomes in the lab and are confident that it is a possible arrangement.”
The experience issues are a significant piece of bringing designing investigation into the field. They were likewise a significant learning opportunity and a potential open door for Zhang and Pawar, who needed to think and react quickly to apply their designing abilities to this present reality.
“We have been in the desert of Texas, where the temperature was more than 100o F; we have been in the meadows of North Dakota, where we saw the primary snow toward the beginning of October; this time we went to Marcellus in the season where the downpour never stops,” said Zhang. “This multitude of encounters not just provides us with a superior understanding of what we have realized and what we are exploring, but additionally enables us to investigate issues when we don’t have each device in our grasp.”