Scientists at the Branch of Energy’s Oak Edge Public Research Center, in a joint effort with NASA, are taking added substance assembly to the last outskirts by 3D printing a similar sort of wheel as the plan utilized by NASA for its mechanical lunar meanderer, showing the innovation for particular parts required for space investigation.
The additively fabricated wheel was demonstrated on the current, light-weight wheels of the Volatiles Researching Polar Investigation Meanderer, or Snake, a versatile robot NASA intends to send in 2024 to plan ice and other expected assets at the south pole of the moon. The mission is planned to assist with deciding the beginning and dispersion of the moon’s water and whether enough could be collected from the moon’s surface to help individuals living there.
While the model wheel printed at DOE’s Assembling Exhibit Office, or MDF, at ORNL won’t really be utilized on the NASA Moon mission, it was made to meet similar plan details as the wheels made for NASA’s Snake. Extra testing is needed to approve the plan and manufacture technique prior to involving this innovation for future lunar or Mars wanderers or taking into account it for other space applications, like enormous primary parts.
Added substance assembly can diminish energy use, material burn-through, and lead time while empowering plan intricacy and the fitting of material properties. MDF is at the cutting edge of this work, fostering innovation for more than 10 years for many applications in the perfect energy, transportation, and assembly areas. MDF scientists printed the wanderer wheel model at ORNL in Fall 2022. A specific 3D printer utilized two lasers and a pivoting fabrication plate to liquefy metal powder into the planned shape.
Common metal powder bed frameworks work in strides: On a machine the size of a cupboard, they rake a layer of powder over a fixed plate. Then a laser specifically dissolves a layer before the plate brings it down somewhat and the interaction rehashes. The printer utilized for the meanderer wheel model is enormous enough for an individual to enter and is remarkable in its capacity to print huge items while the means happen at the same time and persistently, said Peter Wang, who drives the MDF improvement of new laser powder bed combination frameworks.
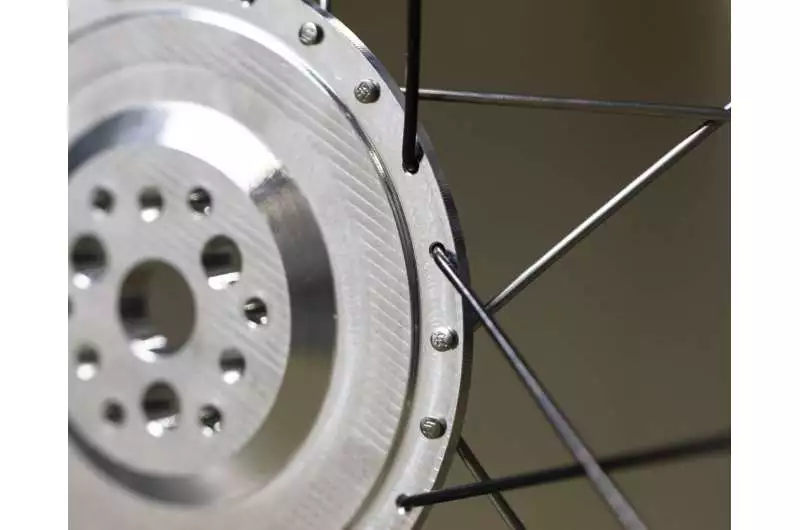
Regardless of empowering a more complicated example and adding locking elements to the wheel, 3D-printing improved and diminished the expense of the wheel plan and made the last gathering simpler. Credit: Carlos Jones/ORNL, U.S. Dept. of Energy
“This decisively expands the creation rate with a similar measure of laser power,” he said, adding that testimony happens half quicker. “We’re just starting to expose what the framework can do. I truly think this will be the eventual fate of laser powder bed printing, particularly on a loose scale and in large-scale manufacturing.”
Wang and his project colleagues have as of late distributed a review on 3D printing and added substance assembly, breaking down the versatility of the innovation for printing parts like electric engines.
Albeit the machine is extraordinary, a key to the progress of the task was specialists’ skill in process computerization and machine control. They utilized programming created at ORNL to “cut” the wheel plan into vertical layers, then, at that point, balanced the responsibility between the two lasers to print equitably, accomplishing a high creation rate, utilizing a computational method as of late submitted for patent insurance.
The model wheel, one of the initial segments created by the framework, exhibits the value of interagency cooperation. “The task with NASA truly impelled innovation forward,” said Brian Gibson, the specialist who drove the meanderer wheel project for ORNL, calling it an achievement. “It was perfect to interface a capacity with a creating need, and the group was eager to make a model part with space investigation applications.”
Made of a nickel-based combination, the model wheel is around 8 inches wide and 20 inches in measurement—a lot bigger than common parts printed with metal powder bed frameworks. It was expected that the capacity to print little mathematical highlights would spread over an enormous workspace. Added substance production empowered more prominent intricacy in the edge plan without added cost or assembly trouble, Gibson said.
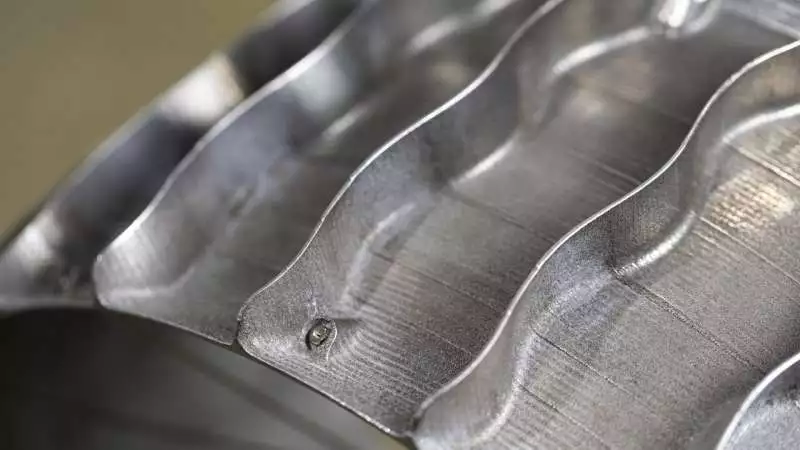
Added substance production permits fine-plan subtleties, like a wavy track on a domed shape, to be integrated into the model lunar wheel. Credit: Carlos Jones/ORNL, U.S. Dept. of Energy
In correlation, the four snake wheels that will stir through moon dust one year from now require different assembling cycles and get-together advances. Snake’s 50-piece wheel edge is kept intact with 360 bolted joints. The assembling system required convoluted and time-serious machining to meet the mission’s thorough necessities.
In the event that NASA testing demonstrates the 3D-printed model to be basically as vigorous as customarily fabricated wheels, future wanderers could rather utilize a solitary printed wheel edge, which took ORNL 40 hours to produce. Through the venture, ORNL and NASA Designs likewise investigated printing exact plan highlights, for example, calculated sidewalls, a domed shape, and a wavy track to build the wheel’s firmness.
These qualities are challenging to consolidate in the ongoing Snake Wheel configuration utilizing conventional creation strategies. Regardless of empowering a more intricate example and adding locking highlights to the wheel, 3D printing rearranged and diminished the expense of the wheel plan and made the last gathering simpler.
“A ton of these wheel highlights were placed in to feature how you can manage added substance fabricating,” said Richard Hagen, a mechanical plan engineer for NASA and added substance producing lab chief at NASA’s Johnson Space Center in Houston. “It allows you effectively to carry out plans that are difficult to execute with conventional tooling or even a customarily machined part.” ORNL’s capacity to print huge items exhibits the capability of added substance fabricating innovation for delivering a lot bigger meanderer wheels for both lunar and Martian missions, Hagen said.
A test is that the particular printer just forms with specific materials—for this situation, a nickel-based composite—so the 3D-printed wheel is half heavier than the aluminum Snake wheel while being printed at a comparable thickness.
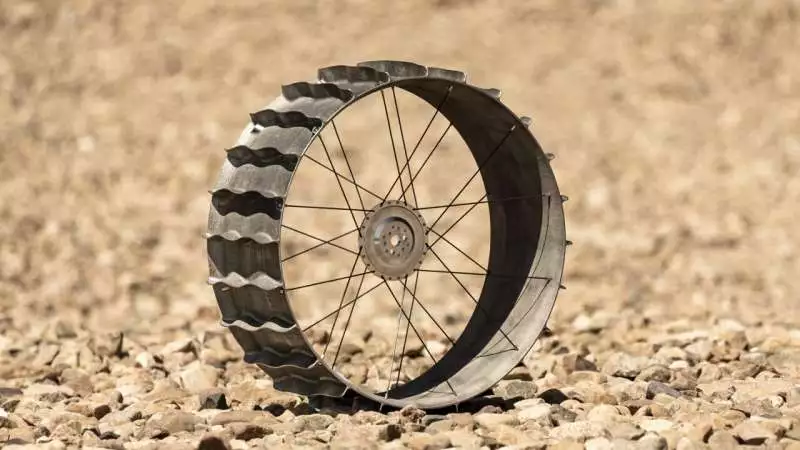
In only a couple of days, ORNL specialists utilized powder bed printing to make this lunar meanderer wheel in light of a NASA plan. Credit: Carlos Jones/ORNL, U.S. Dept. of Energy
NASA intends to test the 3D-printed wheel’s presentation on a meanderer either in the stone yard at NASA’s Johnson Space Center or in a goliath “sandbox” of reproduced lunar shakes and soil at a contracted test office. Evaluators will survey the wheel’s mobility, turning obstruction, sideways slippage, slant climbing, and other execution measurements.
Hagen said added substance fabrication offers the upside of fast plan refreshes because of testing. It can likewise integrate greater intricacy, like a suspension framework, without adding flimsy parts.
Hagen said running research stations put on the moon as a feature of the organization’s Artemis Program will require off-planet production capacity. “Having the option to assemble parts in space for fixes will be significant, in light of the fact that you can’t take an adequate number of extras,” he said. “Powder, pellets, or fiber for printing are much simpler to pack and would take into account greater adaptability.”
“Added substance fabricating offers the adaptability that, assuming you have the feedstock, you could make any new part you really want, whether in space or on the planet,” Gibson said. This is an explanation of how added substance production has created critical interest for a range of substitution needs, from quickly fabricated tooling to hard-to-source castings and forgings. For space investigation and residence, 3D printers could ultimately involve nearby material from the moon or Mars as a feedstock.
More information: Peter Wang et al, Improved Productivity with Multilaser Rotary Powder Bed Fusion Additive Manufacturing, 3D Printing and Additive Manufacturing (2023). DOI: 10.1089/3dp.2022.0288