A method for growing building materials using knitted molds and the root network of fungi has been developed by scientists in an effort to lessen the impact of the construction industry on the environment. Despite the fact that analysts have previously explored different avenues regarding comparative composites, the shape and development imperatives of the natural material have made it hard to foster assorted applications that live up to its true capacity.
The scientists created a composite known as “mycocrete” that is stronger and more flexible in terms of shape and form. This allowed the scientists to grow lightweight and relatively eco-friendly construction materials by using the knitted molds as a flexible framework, or “formwork.”
The paper’s corresponding author, Newcastle University’s Dr. Jane Scott, stated, “Our ambition is to transform the look, feel, and well-being of architectural spaces using mycelium in combination with bio-based materials such as wool, sawdust, and cellulose.” The exploration was completed by a group of fashioners, specialists, and researchers in the Living Materials Exploration Gathering, part of the Center for Biotechnology in the Fabricated Climate at Newcastle College.
“Our goal is to use mycelium in conjunction with bio-based materials such as wool, sawdust, and cellulose to transform the look, feel, and well-being of architectural spaces.”
Dr. Jane Scott of Newcastle University,
Root networks Scientists mix mycelium spores with grains that they can eat and material that they can grow on to make composites using mycelium, which is a part of the root network of fungi. In order for the mycelium to grow and firmly bind the substrate, this mixture is packed into a mold and placed in a warm, humid, and dark environment.
It is dried out once it reaches the right density but before it begins to produce the fruiting bodies that we call mushrooms. Foam, wood, and plastic could all be replaced with something cheaper and more durable using this method. Be that as it may, mycelium needs oxygen to develop, which compels the size and state of regular unbending molds and cutoff points in current applications.
Weaved materials offer a potential arrangement: oxygen-permeable molds that can change from being flexible to being stiff as the mycelium grows. In any case, materials can be excessively yielding, and it is challenging to reliably pack the molds. Scott and her coworkers set out to create a mycelium mixture and a manufacturing system that could take advantage of knitted forms’ potential.
Scott stated, “Knitting is an extremely versatile 3D manufacturing system.” It is light, malleable, and flexible. The ability to knit 3D structures and forms without seams and waste is the primary benefit of knitting technology over other textile processes.
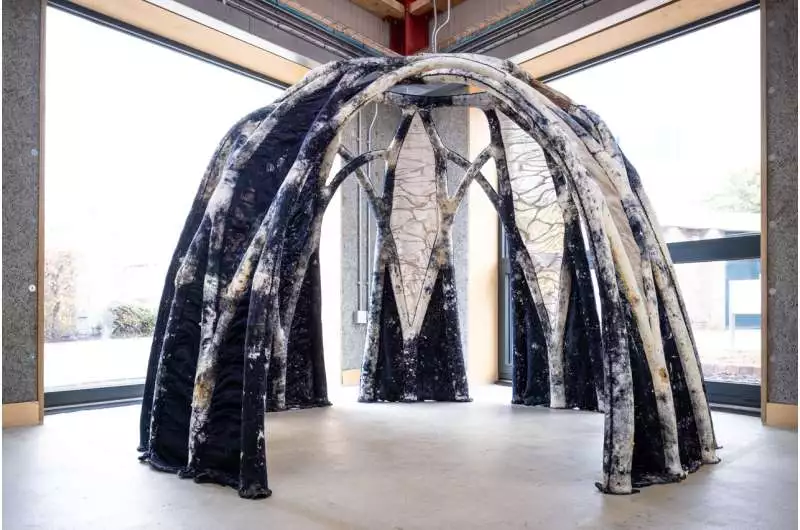
A 1.8-meter-high, 2-meter-wide detached structure made of BioKnit mycocrete utilizing sewed formwork. Credit: Hub for Biotechnology in the Built Environment.
The researchers prepared control samples of conventional mycelium composite and grew them alongside mycocrete, which also contained water, glycerin, paper fiber clumps, paper powder, and xanthan gum. This glue was intended to be conveyed into the sewed formwork with an infusion weapon to further develop pressing consistency. The glue should have been fluid enough for the conveyance framework, but not so fluid that it neglected to hold its shape.
Tubes for their arranged test structure were sewn from merino yarn, disinfected, and fixed to an unbending construction while they were loaded up with the glue, so that adjustments of pressure of the texture wouldn’t influence the exhibition of the mycocrete.
Building what’s to come
Once dried, examples were exposed to strength tests in pressure, pressure, and flexion. The mycocrete samples outperformed mycelium composites grown without knitted formwork and demonstrated greater strength than conventional mycelium composite samples. Also, the permeable weaved texture of the formwork gave better oxygen accessibility, and the examples filled in it shrank, which is not exactly what most mycelium composite materials do when they are dried, suggesting more surprising and steady assembling results could be accomplished.
Due to the flexible knitted form, the team was also able to construct a larger proof-of-concept prototype structure known as BioKnit—a complex freestanding dome constructed in a single piece without joins that could be weak points.
According to Scott, “The mechanical performance of the mycocrete used in conjunction with permanent knitted formwork is a significant result and a step toward the use of mycelium and textile biohybrids in construction.” In order to accomplish a particular objective, we have identified specific yarns, substrates, and mycelium in this paper. Notwithstanding, there is a broad chance to adjust this definition for various applications. Bio fabricated design might require new machine innovation to move materials into the development area.”
More information: Romy Kaiser et al, BioKnit: development of mycelium paste for use with permanent textile formwork, Frontiers in Bioengineering and Biotechnology (2023). DOI: 10.3389/fbioe.2023.1229693