A group of scientists at the University of Massachusetts Amherst and the Georgia Institute of Technology have 3D printed a double-stage, nanostructured high-entropy compound that surpasses the strength and pliability of other cutting-edge additively made materials, which could prompt better execution parts for applications in aviation, medication, energy, and transportation. The work, led by Wen Chen, assistant teacher of mechanical and modern design at UMass, and Ting Zhu, teacher of mechanical design at Georgia Tech, is distributed web-based by the journal Nature.
Throughout recent years, high entropy compounds (HEAs) have become progressively famous as another worldview in materials science. They have at least five components in close equivalent proportions and can be combined in an almost infinite number of novel ways for compound plans.Customary compounds, for example, metal, carbon steel, treated steel, and bronze, contain an essential component joined with at least one minor component.
Added substance production, likewise called 3D printing, has as of late arisen as a strong way to deal with material turns of events. The laser-based 3D printing can create huge temperature angles and high cooling rates that are not promptly open by regular courses. In any case, “the capability of tackling the joined advantages of added substance producing and HEAs for accomplishing novel properties remains generally neglected,” says Zhu.
“Because of their ability to manufacture strong and ductile HEAs, these 3D printed materials are more resilient in resisting applied deformation, which is significant for lightweight structural design for better mechanical efficiency and energy savings,”
Jie Ren, Chen’s Ph.D. student and first author of the paper.
Chen and his group in the Multiscale Materials and Manufacturing Laboratory joined a HEA with a cutting-edge 3D printing method called laser powder bed combination to foster new materials with uncommon properties. Since the cycle makes materials soften and set quickly when contrasted with customary metallurgy, “you get a totally different microstructure that is a long way from balanced” on the parts made, Chen says. This microstructure seems to be a net and is made of rotating layers known as face-focused cubic (FCC) and body-focused cubic (BCC) nanolamellar structures implanted in microscale eutectic states with irregular directions. The progressive nanostructured HEA empowers co-usable twisting of the two stages.
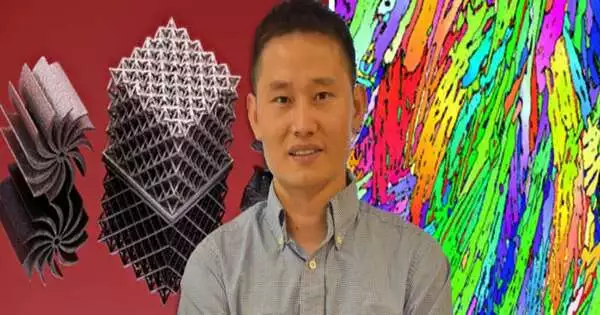
Wen Chen, partner teacher of mechanical and modern design at UMass Amherst, remains before pictures of 3D printed high-entropy compound parts (heatsink fan and octect grid, left) and a cross-sectional electron backscatter diffraction reverse post figure map showing a haphazardly situated nanolamella microstructure (right).
“This strange microstructure’s nuclear revamp leads to ultrahigh strength as well as upgraded pliability, which is phenomenal, on the grounds that normally solid materials will generally be weak,” Chen says. He says that compared with regular metal projecting, “we got practically triple the strength and didn’t lose pliability, yet really expanded it all the while.” “For some applications, a mix of solidarity and pliability is vital. Our discoveries are unique and energizing for materials science and design.
Chen’s Ph.D. understudy and first creator of the paper, says that the capacity to create solid and pliable HEAs implies that these 3D written words are more hearty in opposing applied twisting, which is significant for lightweight underlying models for improved mechanical proficiency and energy savings.
Zhu’s gathering at Georgia Tech drove the computational display for the exploration. He created double-stage gem pliancy computational models to comprehend the robotic roles played by both the FCC and BCC nanolamellae and how they cooperate to give the material added strength and pliability.
“Our recreation results show the shockingly high strength yet high solidifying reactions in the BCC nanolamellae, which are vital for accomplishing the remarkable strength-pliability collaboration of our amalgam. “This robotic comprehension gives a significant premise for directing the future improvement of 3D printed HEAs with uncommon mechanical properties,” Zhu says.
Moreover, 3D printing offers a useful tool to make mathematically intricate and redesigned parts. Later on, bridging 3D printing innovation and the huge amalgam configuration space of HEAs, opens sufficient chances for the immediate creation of end-use parts for biomedical and aviation applications.
Extra examination accomplices on the paper incorporate Texas A&M University, the University of California Los Angeles, Rice University, and Oak Ridge and Lawrence Livermore public labs.
More information: Ting Zhu, Strong yet ductile nanolamellar high-entropy alloys by additive manufacturing, Nature (2022). DOI: 10.1038/s41586-022-04914-8. www.nature.com/articles/s41586-022-04914-8
Journal information: Nature