Shape-memory polymers or shape-moving materials are savvy materials that stand out inside materials science and biomedical design as of late to construct shrewd designs and gadgets. Computerized light handling is a tank photopolymerization-based strategy with fundamentally quicker innovation to print a total layer in a single move toward making brilliant materials.
Fahad Alam and a group of researchers in electrical and PC design and atomic design at the Ruler Abdullah College of Science and Innovation, Saudi Arabia, fostered an easy and quick technique to 3D print shape-memory polymer-based shrewd designs with a computerized light-printing 3D printer and custom gum.
They joined a fluid precious stone (a material that can change its shape with temperature) with tar to acquaint shape-memory properties with straightforwardly 3D-printed thermoresponsive designs while staying away from the intricacy of pitch planning. The group printed the designs with various calculations and estimated the shape-memory reaction. The shape-memory polymers can be helpfully ready for use as brilliant instruments, toys, and meta-materials.
The paper is distributed in the journal NPG Asia Materials.
Shape-memory polymers
Shape-memory polymers belong to a class of double-shape-savvy polymers that can go through mechanical disfigurement and return to their unique shape because of natural boundaries. The shape-memory polymer recuperation relies upon the utilization of outer improvements like intensity, light, power, dampness, and pH changes.
Such materials are shape-moving builds that have acquired significant interest lately because of their flexibility and modern feasibility. The examination group showed 4D printing of shape-memory polymers through computerized light handling, a 3D printing strategy in view of tank photopolymerization. The results featured the reasonableness of 3D-printed complex designs for different applications.
The custom three-dimensional printed structures go through 4-D extension and custom shape changes in a watery climate. Credit: Nature Asia Materials, doi: 10.1038/s41427-023-00511-x
Making a shape-memory impact
The examination group explored the shape-memory impact of the 3D printed tests by concentrating on the shape-drafting and recuperating processes. The technique permitted simple and high-goal printing of complex 3D plans. These developments are helpful across various applications, such as adaptable brilliant patches, size-variable mechanical apparatuses, and deformable toys. In this work, Alam and partners fostered a shape-memory polymer in view of a fluid precious stone blended in with a photocurable pitch to create a semicrystalline polymer and depicted its component of activity in light of past examinations.
The group noticed the inward morphology of the 3D-printed cross segments regardless of fluid precious stones by utilizing filtering electron microscopy. They then noticed the reactions of shape-memory polymers in comparison with their ability to recuperate after load-bearing. The current work showed the impact of 3D advanced light handling to make shape-memory polymers with 4D impacts. The researchers evaluated the shape-memory reaction to show the recuperation point proportion versus time.
Programming and recuperation of the 3D-printed structures and the heap bearing limit of the customized structure. A foldable box. B Savvy bundling transforms structure. C Misshapening and recuperation territories of 3D-printed fiber. D The burden-bearing limit of the modified blossom formed a 3D-printed structure. The manufacture of 3D designs shows the reasonableness of the technique for printing 2D and 3D designs. Credit: Nature Asia Materials, doi: 10.1038/s41427-023-00511-x.
Tunable mechanical properties
The analysts investigated the promising uses of 3D-printed smart memory polymers. To achieve this, Alam and partners determined the mechanical properties of the materials by directing malleable tests on a canine bone example to demonstrate the way that the mechanical properties of written words can be tuned by controlling the state of the cross-section structures.
They affirmed the mechanical tunability of shrewd materials by directing limited component reproductions and contrasted the trial results and malleable tests from the limited component examination. The mechanical exhibitions of the 2D cross sections were explored and anticipated by means of reproduction. In light of the adaptability and stretchability, Alam and the group tried the examples for strain testing and for joint movement detection applications.
To work with joint movement by means of polymer coordination, the researchers applied a nano-silver-based conductive covering as a cathode, which required further improvement of the printing boundaries. The researchers estimated the progression of electrical obstruction by extending and packing the design to work with the development of patients.
The consequences of opposition estimation of the pre-arranged cross-section cathode fix showed its true capacity for use as a savvy fix for joint-development detection; this can be applied to a human knee, elbow joint, counterfeit appendage, or genuine appendage to detect development. Such terminal patches can be modified to the size of the patient under simple and quick assembly processes.
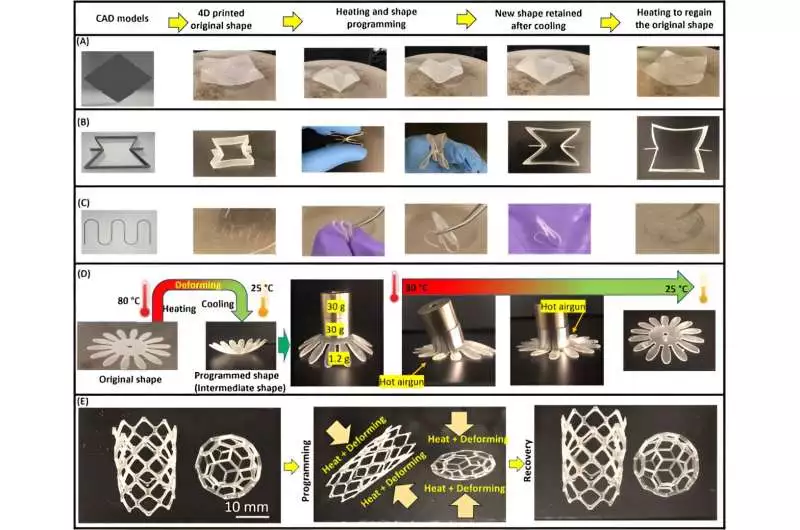
Micrographs of the cross-part of 3D-printed tests were seen under SEM. A Sap in particular and B LC blended in with gum. (a) and (b) are the amplified places of the micrographs featured with specked yellow lines from (A) and (B), individually. Credit: NPG Asia Materials (2023). DOI: 10.1038/s41427-023-00511-x
Outlook
Along these lines, Fahad Alam and his group introduced a technique for 3D print-savvy materials by first involving shape-memory polymers for simple and quick production through computerized light handling. The researchers modified the 3D-printed objects to make structures that changed with time; this is known as 4D printing. They accomplished this by joining fluid precious stones with a pitch and printing it by utilizing a business work area printer. The specialists utilized the technique to produce various complex items, including cross-section patches, foldable toys, brilliant bundling, and mechanical wrenches.
The researchers exposed these items to heat to briefly change their shape and for resulting shape recuperation applications. The group utilized ductile tests to show the customizable idea of shape-memory polymers and to meet explicit applications in biomedical design. Such 3D-printed grid patches are appropriate for strain detection in joint development applications. The specialists kept the progressions in electrical obstruction from the 3D-printed brilliant fix to identify the development in fake appendage joints and arms of patients.
More information: Fahad Alam et al. Swift 4D printing of thermoresponsive shape-memory polymers using vat photopolymerization, NPG Asia Materials (2023). DOI: 10.1038/s41427-023-00511-x